الحار منتجات
ملكنا الإخبارية
mill operation in cement raw
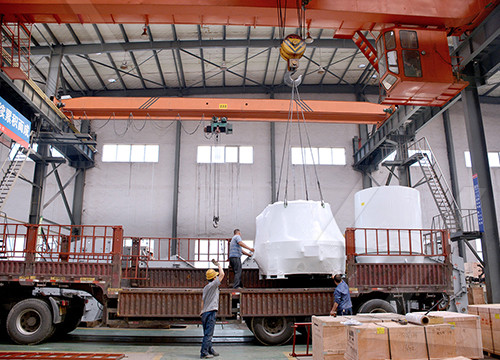
Optimization of Cement Manufacturing Process ScienceDirect
198781 Cement manufacturing process is now operated with the aid of various control systems, such as raw meal composition control, kiln control and mill control. Those systems have greatly contributed to achieve uniformity of quality as well as cost
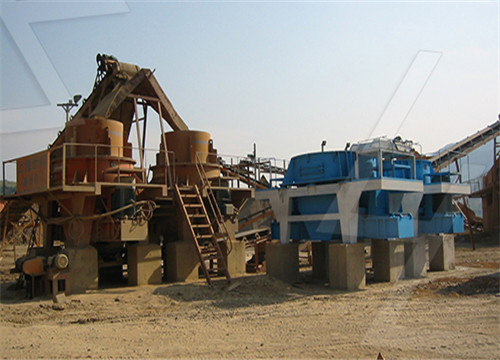
Reducing energy consumption of a raw mill in cement industry
201261 The study indicates that for a dry type cement production process, the carbon dioxide emission intensity for kiln feed preparation process is about 5.4 kg CO 2

Analysis of material flow and consumption in cement
2016120 Recycling waste gas discharged from raw and cement mills should be the focus. Keywords Material flow Material efficiency Mass balance Cement production
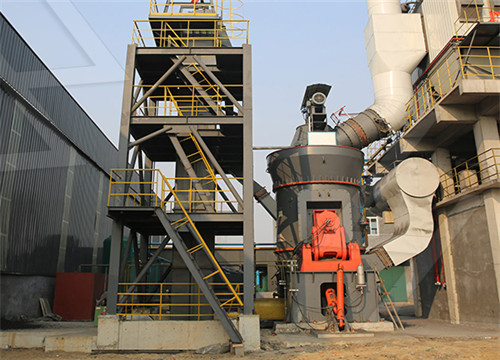
A Survey and Analysis on Electricity Consumption of Raw Material Mill
2021122 At present, the raw material preparation process of new drying-process cement production enterprises mainly includes middle unloading drying tube mill raw
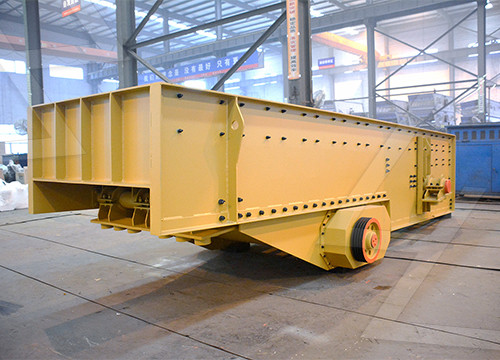
Thermodynamic Performance Analysis of a Raw Mill System in a Cement
201811 The transfer of heat between the inlet layer of the raw mill and the environment is the most generally encountered operation in the component design
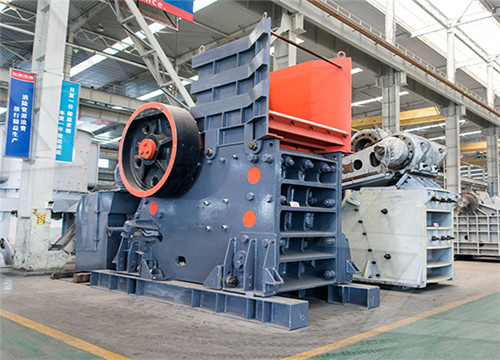
(PDF) Thermodynamic Analysis of Raw Mill in Cement
2018910 The simulator was used for the thermodynamic performance of a raw mill (RM) and raw materials preparation unit in a cement plant in Nigeria using actual
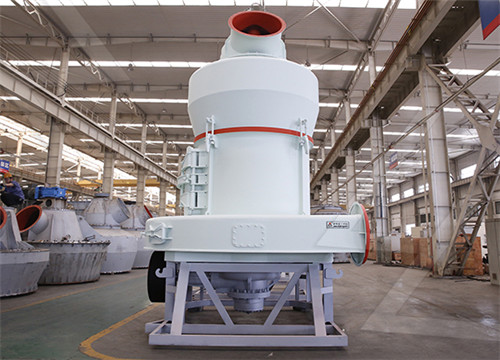
Modeling of energy consumption factors for an industrial cement
202259 Lin, X.Liang, J. Modeling based on the extreme learning machine for raw cement mill grinding process. in Proceedings of the 2015 Chinese Intelligent Automation
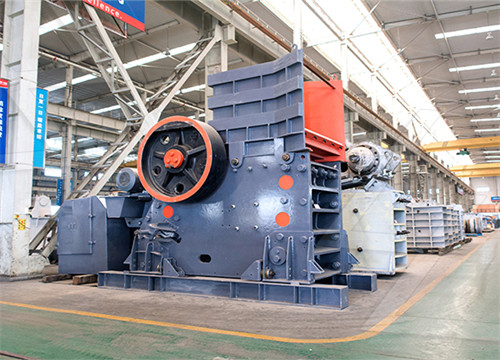
Energy-Efficient Technologies in Cement Grinding
2016105 Roller mills are operated with throughput capacities of more than 300 t/h of cement raw mix (Loesche mill, Polysius® double roller mill, Pfeiffer® MPS mill). Loesche roller mill and Polysius® roller mills are
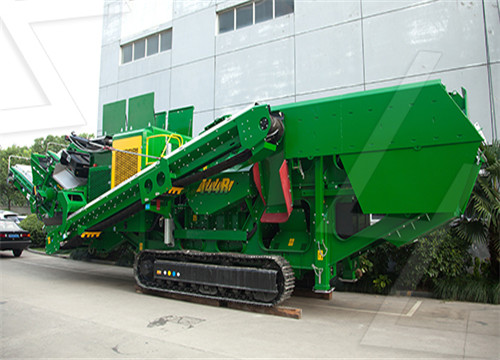
Full article: Evaluation of optimization techniques for
The cement raw mill is the primary piece of equipment used in the modern cement industry for the raw meal production process. As a result, it is critical to investigate the exergy
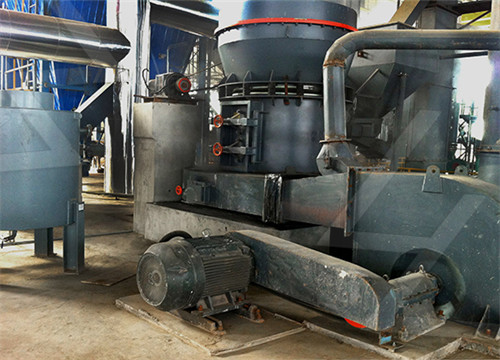
Raw Material Drying-Grinding Cement Plant Optimization
Ball mills for cement raw material and coal equipped with a drying compartment adequately air swept with hot gas (2.5-3.5M/sec above the ball charge), can handle moisture about 8%. Fully air- swept mills (5-6M/sec) can dry up to 12-14% moisture. Grinding Operation Objectives and KPIs: Highly energy intensive unit operation of size reduction in
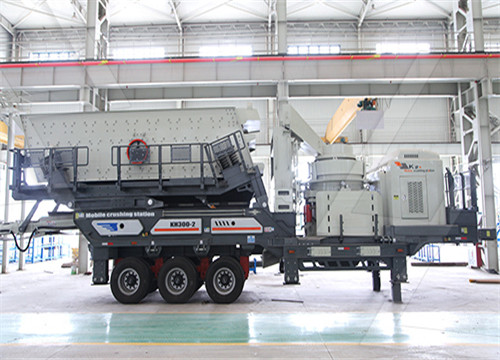
A data-driven decision-making framework for online control
202051 Introduction. Vertical roller mill (VRM) is a type of heavy-duty and energy-intensive grinding equipment for many industries, such as cement, steel and chemical industries. It is used to grind slag, nonmetallic ore and other block and granular raw materials into required powder materials. The fine powders can be used as raw materials
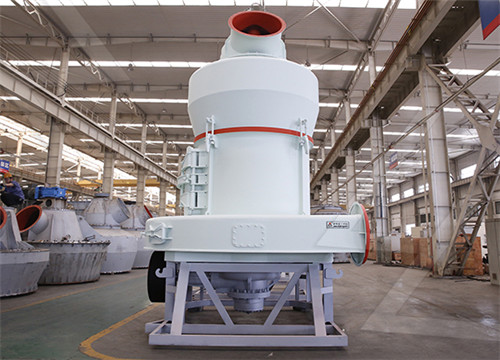
Operational parameters affecting the vertical roller mill
201741 Abstract. Vertical roller mills (VRM) have found applications mostly in cement grinding operations where they were used in raw meal and finish grinding stages and in power plants for coal grinding. The mill combines crushing, grinding, classification and if necessary drying operations in one unit and enables to decrease number of equipment
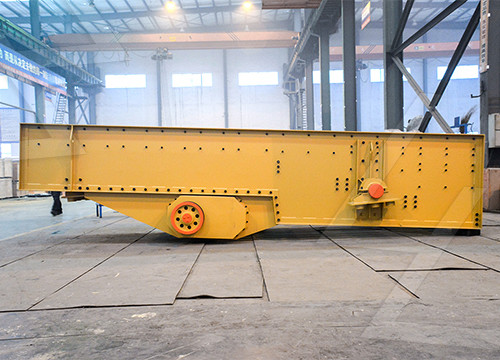
Thermodynamic Performance Analysis of a Raw Mill System in a Cement
201811 The energy efficiency equation of a raw mill system in the cement process is defined as: (44) η R M = m 2 h 2 + m 3 h 3 m 1 h 1 + m 4 h 4. 3.6. Exergy Efficiency. The exergetic efficiency analysis provides some significant indicators about the process and its parts for efficient use.
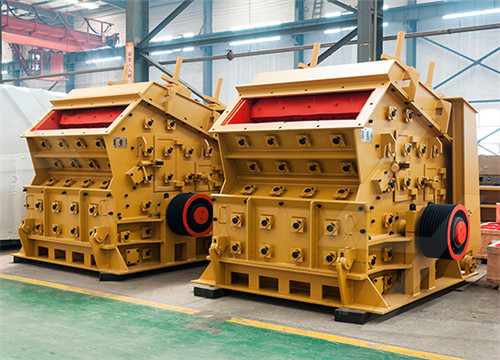
Technological Energy Efficiency Improvements in Cement Industries
2021330 The cement industry is highly energy-intensive, consuming approximately 7% of global industrial energy consumption each year. Improving production technology is a good strategy to reduce the energy needs of a cement plant. The market offers a wide variety of alternative solutions; besides, the literature already provides reviews of
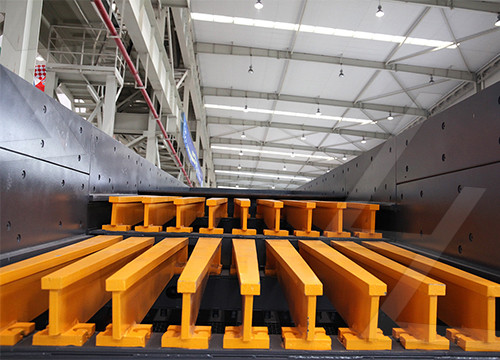
Loesche vertical roller mills for the comminution of ores and minerals
2001101 Since mid 2000 a LM 50.4 has been in operation for the comminution of a phosphate carrying pyroxenite ore with a capacity of 825 t/h at a D80 of 480 μm. References. Brundiek, 2000. H. Brundiek. The world's largest vertical roller mills for producing cement raw meal at the start of the 21 st century. Cement—Lime—Gypsum
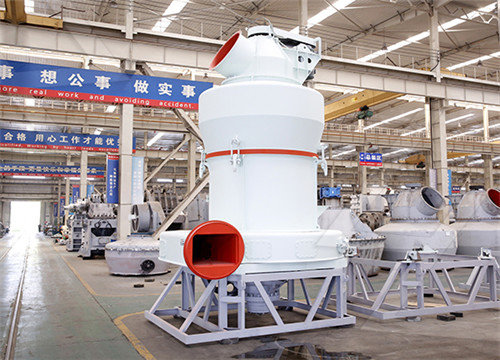
Parametric Studies of Cement Production Processes Hindawi
The cement industry is one of the most intensive energy consumers in the industrial sectors. The energy consumption represents 40% to 60% of production cost. Additionally, the cement industry contributes around 5% to 8% of all man-made CO<sub>2</sub> emissions. Physiochemical and thermochemical reactions involved in cement kilns are still not well
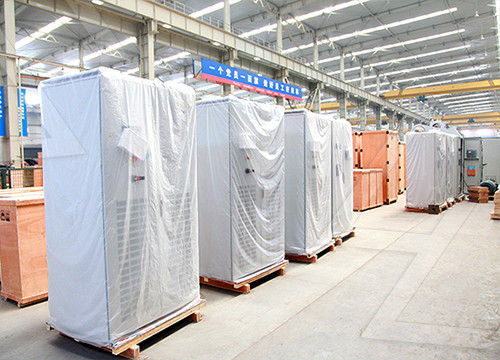
Vertical Raw Mill for Cement Raw Meal Grinding in Cement
Vertical raw mill is important equipment widely used in the cement raw meal (cement raw materials) grinding section of the cement production process in cement plant.Because the vertical raw mill is the use of roller grinding principle to crush materials, its vertical raw mill operation is more efficient and energy-saving, product output is more stable, so in
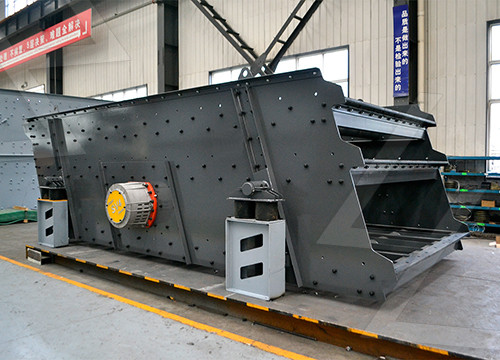
Heat Integration in a Cement Production IntechOpen
20181010 The kiln has an operation capacity of 90 t/h and upper bound of 110 t/h. A total of 57 t/h of the clinker is produced inside the kiln. For the heating of the raw mill, kiln raw meal, and a coal mill, hot flue gases from the kiln are deployed. Gases exit from a preheating tower with a temperature at about 370°C.
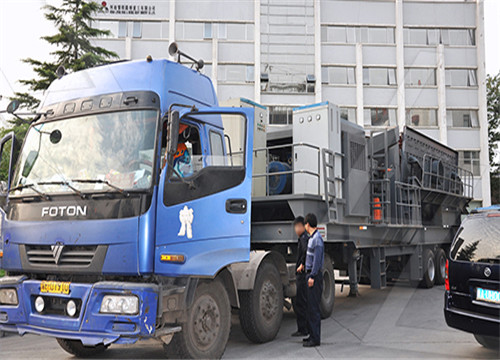
(PDF) Effects of Mill Speed and Air Classifier Speed on
2021629 Optimum performance of ball mill could potentially refine Blaine fineness, thereby improving the cement quality. This study investigates the effects of separator speed and mill speed on Blaine
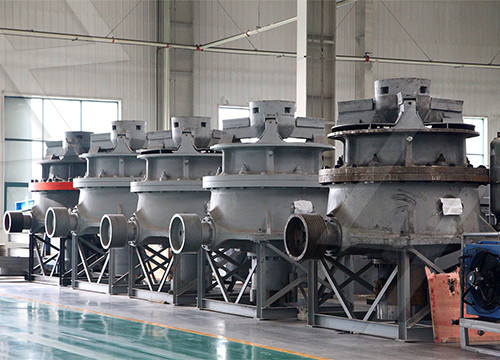
(PDF) Effects of Mill Speed and Air Classifier Speed on
2021629 Nowadays, ball mills are widely used in cement plants to grind clinker and gypsum to produce cement. The research focuses on the mill speed as well as air classifier speed effect on the two
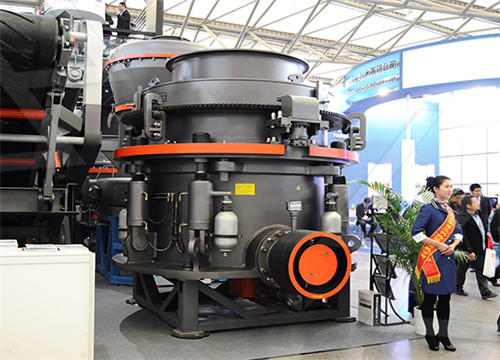
A Review on Pyroprocessing Techniques for
202029 The raw materials used in cement manufacturing are also limited and sometimes rare. The proportioned raw materials are then transported by a conveyor belt to the raw mill to be ground into the
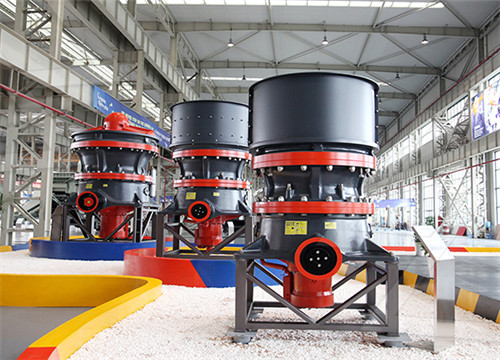
Cement Finish Milling (Part 1: IntroductionHistory)
2019122 Size reduction is a critical process at numerous stages of cement manufacture mainly to ensure homogeneity and reactivity of the cement, raw mix, and fuels. The finish mill system in cement
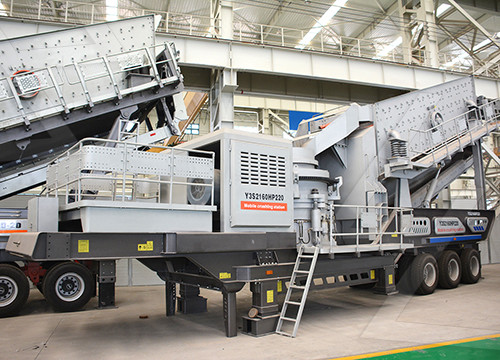
Grinding process optimization IEEE Xplore
2017619 As a world-wide leader in grinding solutions for the cement industry and understanding the changing needs of cement producers and how to tailor solutions to meet those needs. Optimizing output, improving efficiency, and reducing CO2 emissions while keeping investment costs to a minimum are common challenges that the modular vertical
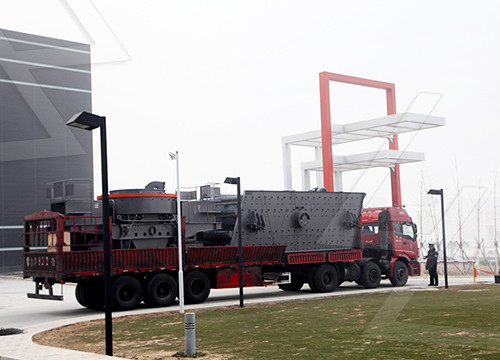
Job Safety Analysis for Various Operations in Cement
202125 After crushing, the raw materials are transported to the plant by conveyor. Before homogenized, the plant stores the material. Too finely ground, the materials are transferred to the raw mill, to produce raw mix. The raw mix is preheated before it goes into the kiln, and by the flame, it can be heated to 2000 °c to produce clinker.
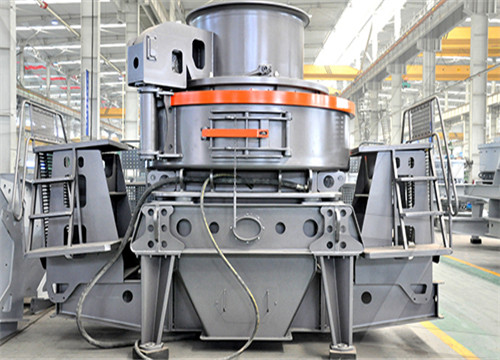
Machine learning applications and process intelligence for cement
202111 1. Introduction. Cement grinding is a key process in the cement industry. During this phase, gypsum and mineral or artificial raw materials (e.g., pozzolan, ash, limestone) are added to the clinker (basic raw material for cement production) and, then grinded in special mills until a very small grain size is achieved.
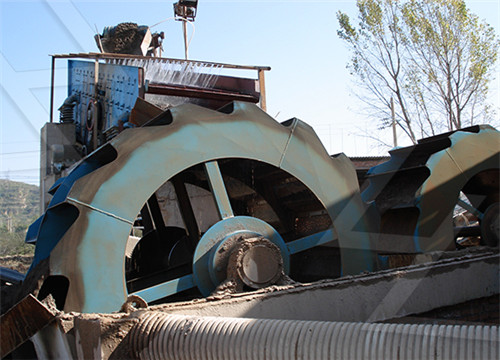
Vertical Raw Mill for Cement Raw Meal Grinding in Cement
Vertical raw mill is important equipment widely used in the cement raw meal (cement raw materials) grinding section of the cement production process in cement plant.Because the vertical raw mill is the use of roller grinding principle to crush materials, its vertical raw mill operation is more efficient and energy-saving, product output is more stable, so in
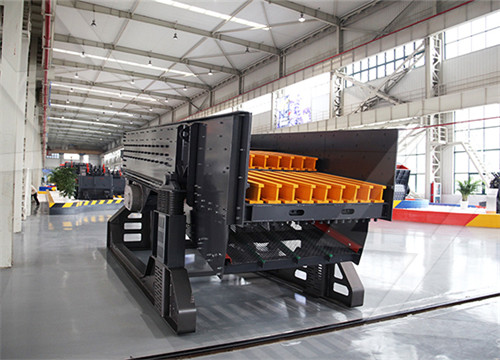
Ventilation Prediction for an Industrial Cement Raw Ball
2021611 the data were collected from one of the Raw Material ball mill circuits (line 1) of the Ilam cement plant (Figure1). This plant has 2 lines for cement production (5300 t/d). The ball mill has one component, 5.20 m diameter, and 11.20 m length with 240 t/h capacity (made by PSP Company from Prerˇ ov, Czechia).
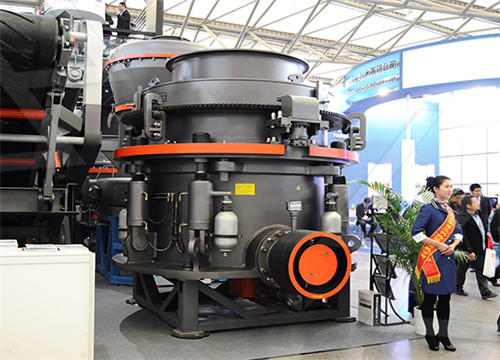
Review on vertical roller mill in cement industryits
202111 The raw mill is either a Ball mill with two chambers or Vertical roller mill with inbuilt classifier. The hot gases from the pre heater enter the mill and are used for drying material in the mills. so vertical roller mills can also grind the white cement raw material [15], Operation • Mill Gas Flow The three roles of the gas flow in
صخرة ج التسرع آلة دائرة
مطحنة في السودان من باجاج مع السعر
منصات الفرامل الأحذية المحمولة سلسلة lm العمودي مطحنة
قدم المطحنه gyratory
الشاشة الخطية لتعدين الذهب
كينيا تعويم الفضة محطة إثراء خام للبيع
حلول المعدنية كوم
منة مطحنة الدائرة المغلقة المفتوحة
إجمالي غسل النظام الهند
الألعاب النارية بضغط الغاز
تعدين الرمال الناعمة
میانمار سنگ معدن روی، سرب
انفجار شن و ماسه دستگاه چرخ
ثمن المطاحن الصغيرة
تستخدم كسارة الصخور عن الأسعار
طحن مقاعد المطاحن الدنمارك
triturador de cone primário móvel para venda nas filipinas
الرسم المسمى محطم الرائدة أسعار المشتركة الحجر
الفك محطم للبيع المستخدمة
تنزانيا حجر الجير كسارة
التكسير الثابت مهتم
مطحنة تزهر مستعملة للبيع
معدات مصانع معالجة الذهب الصغيرة
مصانع معالجة التعدين الكاملة المستكشف
سنگ شکن سنگ معدن به پودر
اندونيسيا كسارة مصنعين مصنعين اندونيسيا
حول لدينا
تأسست شركة Henan Lrate للعلوم والتكنولوجيا المحدودة التي تصنع معدات التكسير والطحن الكبيرة والمتوسطة الحجم في عام 1987. وهي شركة مساهمة حديثة مع البحث والتصنيع والمبيعات معًا.
على مدار أكثر من 30 عامًا ، تلتزم شركتنا بنظام الإدارة العلمية الحديث والتصنيع الدقيق والريادة والابتكار. الآن أصبحت LIMING رائدة في صناعة تصنيع الآلات المحلية والخارجية.