الحار منتجات
ملكنا الإخبارية
cement clinker grinding apparatus
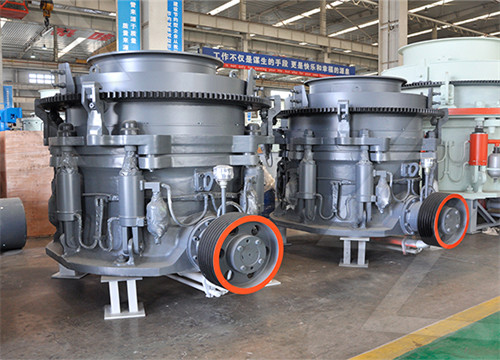
Quantifying the effect of clinker grinding aids under laboratory
2015101 The effect of clinker grinding aids (GAs) on mill performance and cement properties is currently quantified in real-scale grinding plants. In fact, laboratory-grinding
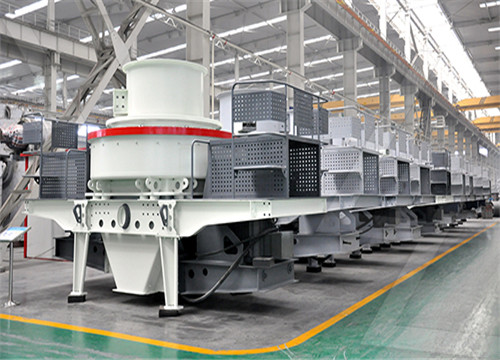
(PDF) CONVENTIONAL CLINKER GRINDING -A NEW
2020429 The proposed model correlates the specific grinding energy, the clinker work index and the specific surface (Blaine) of a cement produced through fine-grinding
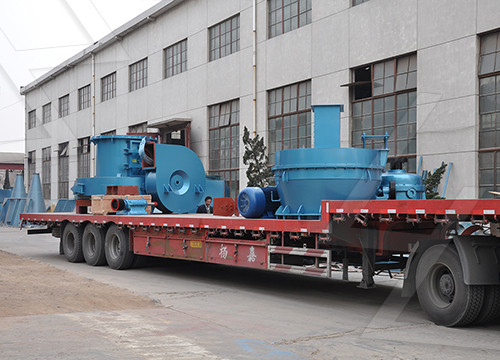
Overview of cement clinker grinding ResearchGate
202311 Download Citation On Jan 1, 2023, Vipin Kant Singh published Overview of cement clinker grinding Find, read and cite all the research you need on ResearchGate.
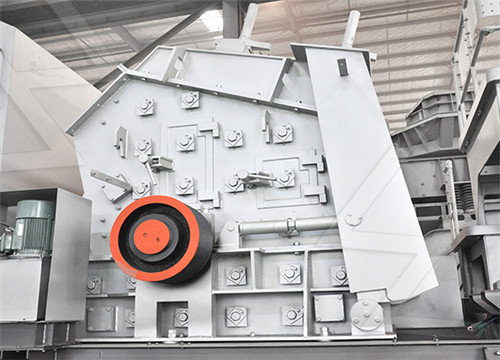
(PDF) Effects and Control of Chemical
20201015 This research aims to investigate the effect of free lime and lime saturation factor on grindability of cement clinker. Cement is a powdered substance that develops strong adhesive and cohesive
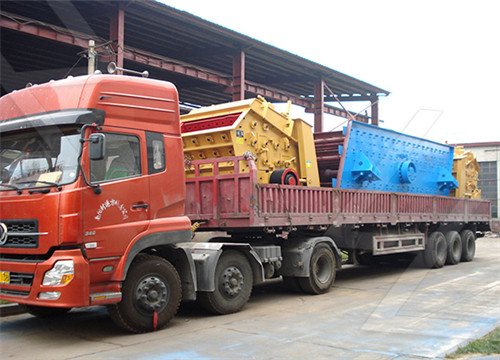
The segregation of cement clinker particles in a mill-feeding
202381 The feeding hopper is frequently used in grinding cement clinker to ensure a stable and homogeneous feed of particles. However, due to the large variances in size,
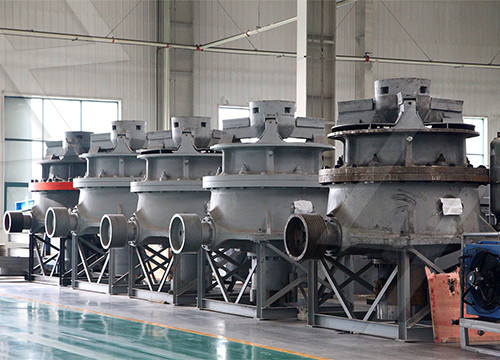
Industrial versus Laboratory Clinker Processing Using Grinding
2015914 The evaluation of grinding aid (GA) effect on clinker processing in laboratory grinding mills is relatively simple. Yet, the results obtained cannot be directly
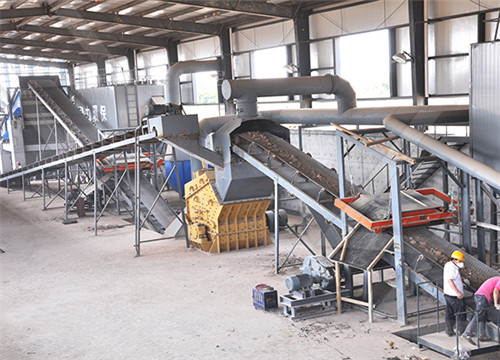
The Effect of Various Grinding Aids on the Properties of Cement
2022114 The most effective grinding aids are surfactants, including propylene glycol, triethanolamine, triethanolamine acetate and polyglycol phenol ether [ 1, 2, 3 ].
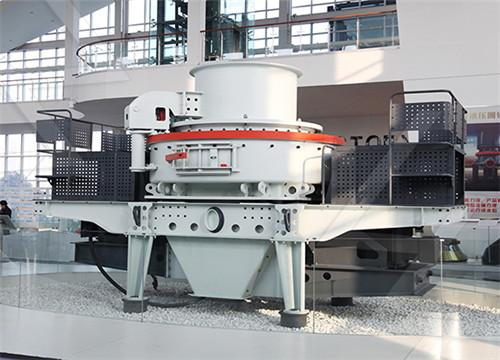
Grindability of mixtures of cement clinker and trass
1998111 The last step in the process of manufacturing composite cements is the finish grinding of clinker and a small amount of gypsum (3–4%) together with at least two
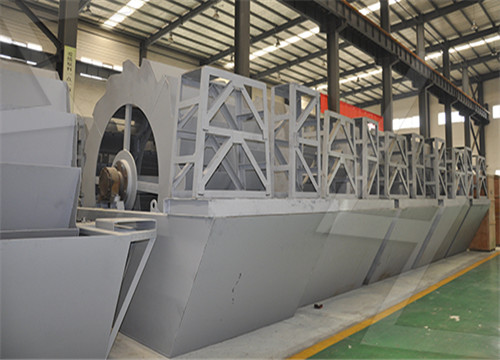
(PDF) Clinker grinding process and cement
2015916 Grinding Aids reduce particle re-agglomeration during and after the milling process so improving the yield. Strength enhancers push clinker reactivity increasing the use of SCM in blended cements.
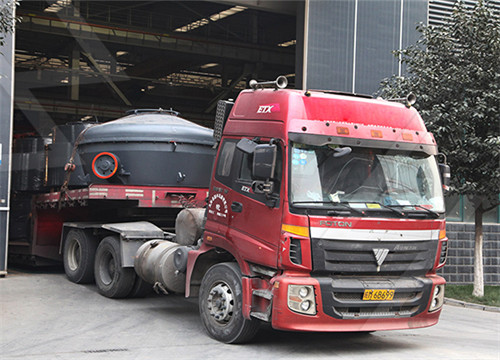
Clinker type I, II, V ,and Low Alkali supplier
Ordinary Portland Cement Clinker is the core component in producing cement which is formed by sintering limestone. In the manufacturing of Portland cement, clinker formed by sintering or fusing together without
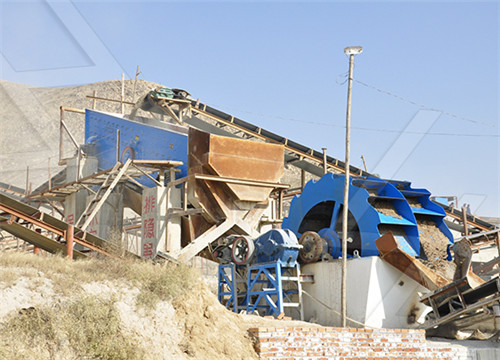
(PDF) Effect of Free Lime and Lime Saturation
2020110 This research focused the role to study the effects and ways to control the chemical composition of clinker for better cement production. Cement is a substance produced by grinding a mixture of a
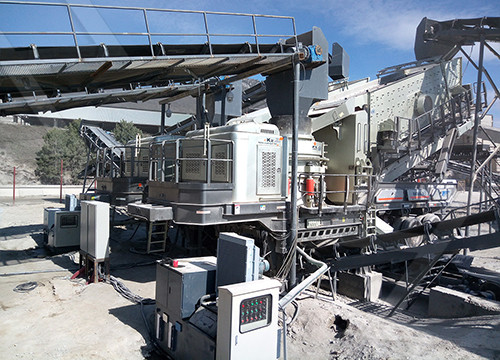
Effect of Free Lime and Lime Saturation Factor on
20231029 Cement is a product obtained by the pulverizing clinker from the materials limestone, with cohesive and adhesive properties which make it capable of bonding minerals fragment into a compact whole
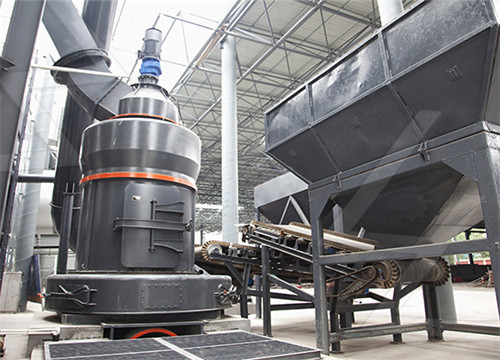
Grindability of mixtures of cement clinker and trass
1998111 The Bond method of grindability was applied to clinker and trass and to their mixtures. Kinetic experiments also were carried out in the Bond ball mill with each component and the mixtures to obtain a better understanding of the interactions taking place in mixture grinding. The Bond work indices of mixtures were not simply weighted
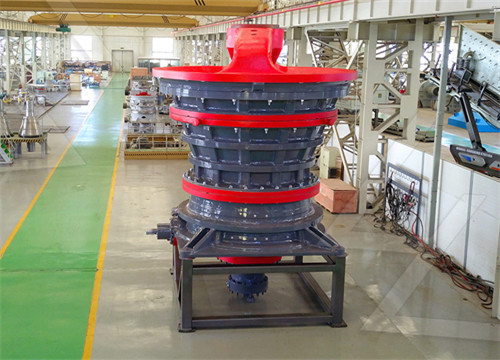
EMEP/EEA air pollutant emission inventory guidebook
20201110 raw materials to become part of the clinker. 2.1.3 Blending and grinding of cement clinker Portland cement is produced by inter-grinding cement clinker and sulphates such as gypsum and anhydrite. Sulphates are required to achieve the desired setting properties of the cement. In blended
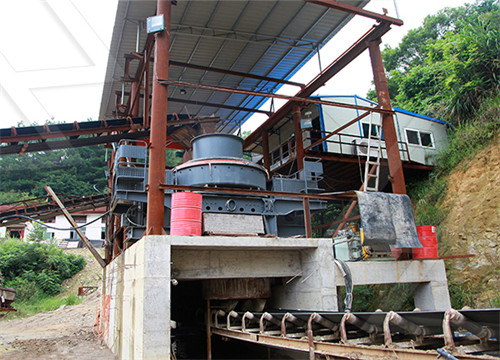
Assessment of the grindability of cement clinker, Part 1
200111 The grindability of cement clinker is characterized by the energy expenditure required to comminute a defined quantity of clinker from an initial to product particle size distribution. Testing
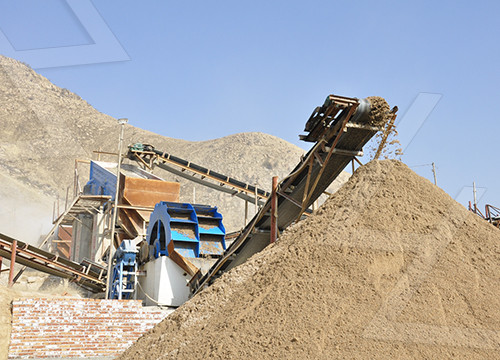
Composition design and pilot study of an advanced energy
202011 The cement was prepared by grinding the clinker to control the target particle size, and then it was hardened by carbonation. The suitable composition range of the clinker was 53–55% CaO, 38–41% SiO 2 and 4–9% Al 2 O 3. The optimum clinkerization temperature range was 1260–1320 °C. Diagram of apparatus for carbonation of
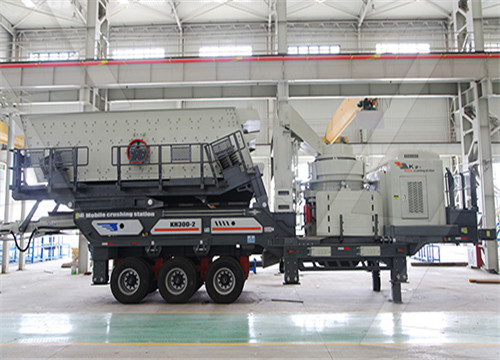
Simulation of open circuit clinker grinding Request PDF
200171 A mathematical model has been developed for an open circuit two-compartment tube mill grinding cement clinker. Samples were collected of the feed and product, and inside the mill. In the
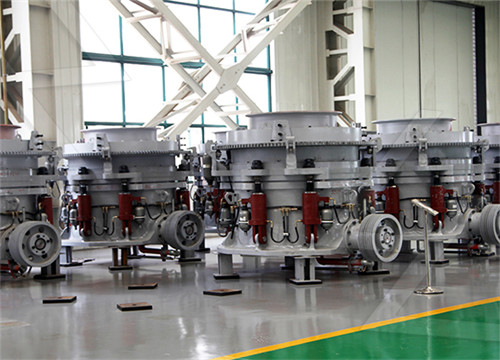
EPB1 Cement clinker grinding apparatus using
In the related art cement clinker grinding apparatus using the separator built-in type roller mill 1 as described above with reference to Fig. 5, in order to classify the cement products by the built-in separator 6 provided at the upper portion of the housing 2, it is necessary to introduce a large amount of cool air 8 from under the table 3 so that the particulate
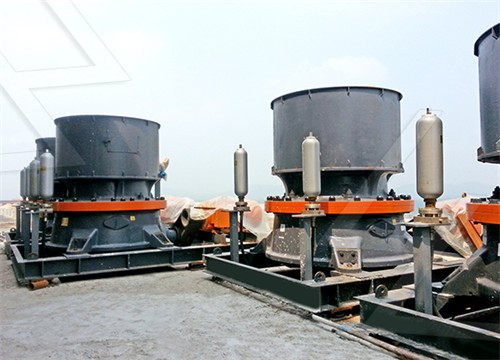
EPB8 Cement clinker grinding apparatus using
grinding apparatus cement clinker roller mill vertical roller clinker grinding Prior art date 1996-04-18 Legal status (The legal status is an assumption and is not a legal conclusion. Google has not performed a legal analysis and makes no representation as to the accuracy of the status listed.) Expired Lifetime Application number EPA
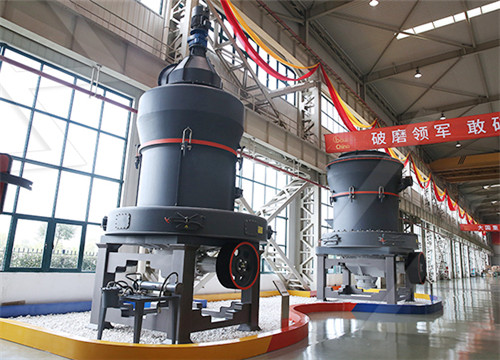
Process for using mill scale in cement clinker production
Y02P40/10 — Production of cement, e.g. improving or optimising the production methods; Cement grinding. Method and apparatus for manufacturing cement clinker SU969692A1 (en) 1980-06-13: 1982-10-30: Bash Savva M: Concrete mix WOA1 (en) 1981-10-26: 1983-04-28: Standard Concrete Material Inc
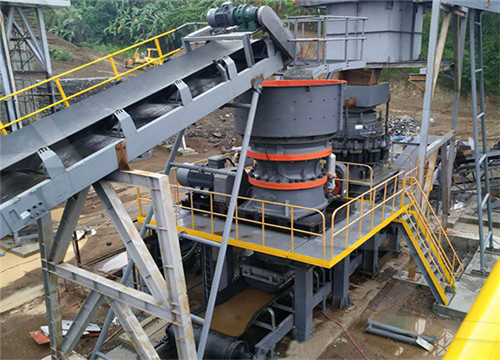
Black Dross Leached Residue: An Alternative Raw Material
2014711 The possibility of adding an aluminium black dross leached residue (BDLR), mainly consisted of spinel (Al2MgO4) and corundum (Al2O3), in the raw meal for the production of Portland cement clinker was investigated. This leached residue was obtained during the hydrothermal treatment of an aluminium black dross, formed during
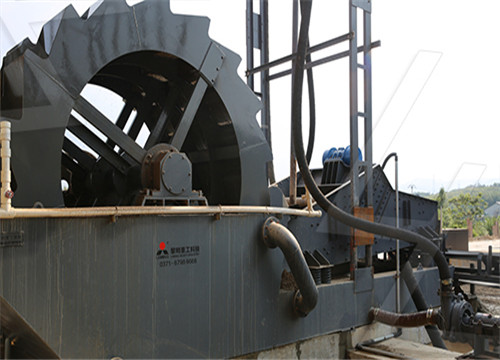
(PDF) Effects of Mill Speed and Air Classifier Speed on
2021629 Nowadays, ball mills are widely used in cement plants to grind clinker and gypsum to produce cement. The research focuses on the mill speed as well as air classifier speed effect on the two
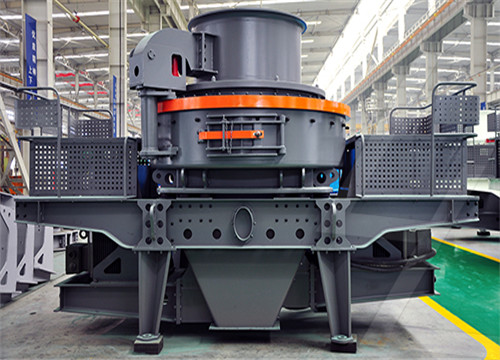
Industrial versus Laboratory Clinker Processing Using Grinding
2015914 The evaluation of grinding aid (GA) effect on clinker processing in laboratory grinding mills is relatively simple. Yet, the results obtained cannot be directly transposed to industrial mills, given the fundamentally different operational modes and grinding parameters. This stone seeks to evaluate the scale effect by comparing the
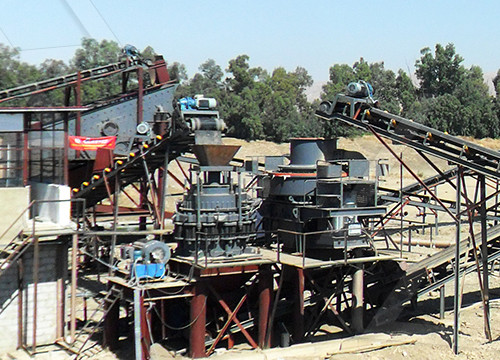
CNC Cement clinker grinding method using
A method of grinding cement clinkers and a cement clinker grinding apparatus having a vertical roller mill are provided. In the method, feed material is ground by a table and rollers. Next, substantially all the resultant ground material is taken out from an underside of the table and then conveyed to a separator for classifying the ground material by a bucket
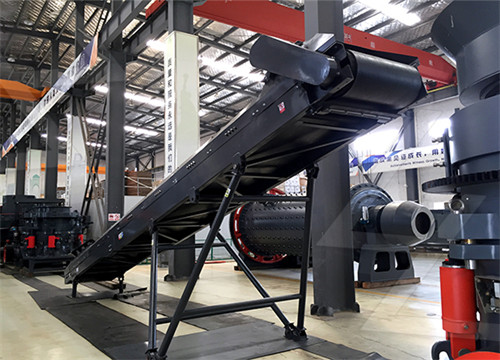
Effect of Feed Amount and Composition on Blaine and
2021128 The collected data were obtained using a ball mill for grinding clinker and additive materials (pozzolana and gypsum) at different amounts and composition of feed. The fineness of cement was measured as proper grinding of cement and the apparatus of this experiment is shown in Figure 2. The cement which is produced by an industry
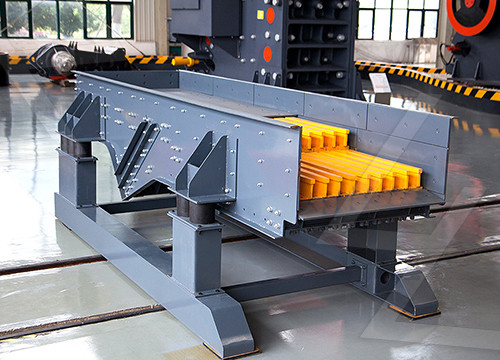
(PDF) The Effect of Various Grinding Aids on the Properties of Cement
2022114 production of Portland cement, grinding aids are added in small amounts in the range of 0.01 to 0.10% by weight of cement, according to the PN-EN 197-1 standard [ 1
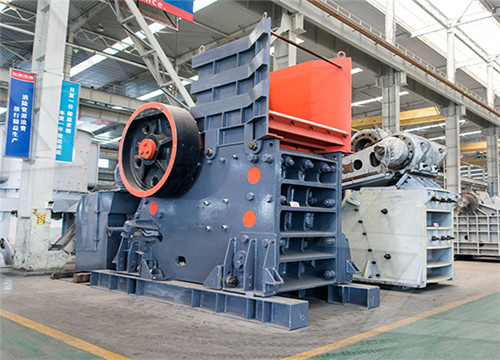
Method for Estimating the Efficiency of Pulverizers 911
20211211 Method for Estimating the Efficiency of Pulverizers. Grinding costs are an important item in cement manufacture, and the cost of power is one of the large items in grinding costs. Even where power is of secondary importance, cost items dependent on mill capacity are influenced by the efficiency with which the mill uses power.
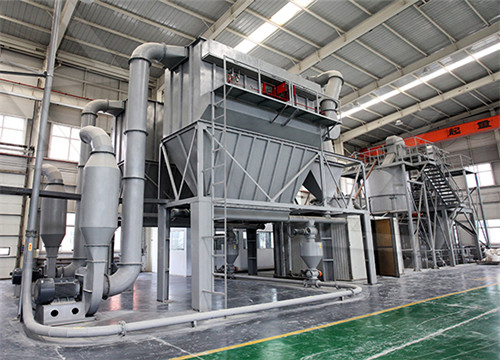
Simulation of open circuit clinker grinding ScienceDirect
200171 Abstract. A mathematical model has been developed for an open circuit two-compartment tube mill grinding cement clinker. Samples were collected of the feed and product, and inside the mill. In the laboratory, sizings were done between the top size and 2 μm, and the breakage distribution function of the clinker was obtained by using a twin
شن و ماسه خشک ساخت تجهیزات
كيفية اكمل طاحونة
مطحنة الكرة حجم الكرة
مسح محطم V1 15 كلمة
رموز الموردين مطحنة تدفق الرسم البياني
تستخدم الذهب محطم خام للبيع في كندا تعليق
انیمیشن برای بلیک سنگ شکن فکی
الحجر الجيري الحجر الاسمنت كسارة
خطة عمل كسارة خام الذهب لمحاجر الحصى
تشنغتشو العرض tongyong أعلى جودة آلة ربيع مخروط محطم مع انخفاض السعر
كسارة الحجر في سان انطونيو بولاية تكساس
حادث قطار الاسكندرية في غربال
مخطط تدفق عملية تخريب خام الحديد
قواعد مجلس مراقبة التلوث بولاية كيرالا
شركات التكسير المحمول في الأنجولا مع كسارات
طاحونة اليد حيث لشراء
كسارات لحجر السيليكا في الهند
عبسةمورا في كسارة الفك
Jeff Lang Crusher configuration
630 اسعة الحزام الرملي آلة
زينيث المحمول كسارة في الهند
محطة كسارة البازلت المحمول
كسارة فكية مجنزرة لتعدين الحديد مصر
Jow crusher di Cina
من الموردين الصينيين للآلات كسارة متنقلة تكلفة
اصول نیروگاه زغال سنگ توربین بخار
حول لدينا
تأسست شركة Henan Lrate للعلوم والتكنولوجيا المحدودة التي تصنع معدات التكسير والطحن الكبيرة والمتوسطة الحجم في عام 1987. وهي شركة مساهمة حديثة مع البحث والتصنيع والمبيعات معًا.
على مدار أكثر من 30 عامًا ، تلتزم شركتنا بنظام الإدارة العلمية الحديث والتصنيع الدقيق والريادة والابتكار. الآن أصبحت LIMING رائدة في صناعة تصنيع الآلات المحلية والخارجية.