الحار منتجات
ملكنا الإخبارية
ball mill and heat build up and coating
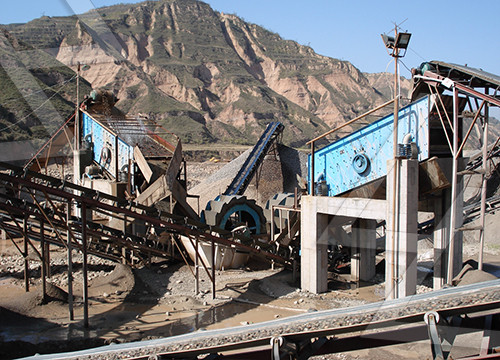
Analysis on energy transfer during mechanical coating and
2013610 To investigate energy distribution and transfer during mechanical coating and ball milling, mechanical coating of Cu coatings on Al 2 O 3 balls and a series of
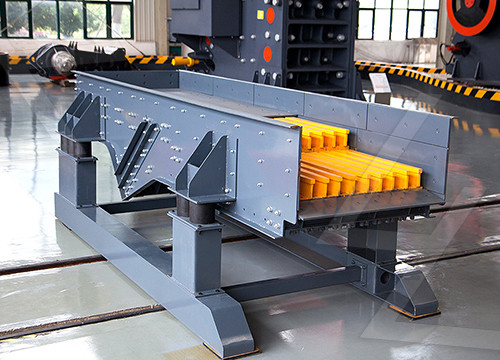
Influence of preliminary heat treatment and ball milling of
202011 , A.V. Smirnov a Add to Mendeley https://doi/10.1016/j.matpr.2019.12.090 Get rights and content Abstract −3 MPa,
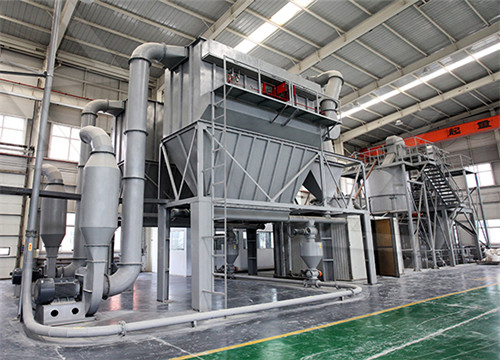
Materials Development Using High-Energy Ball Milling: A
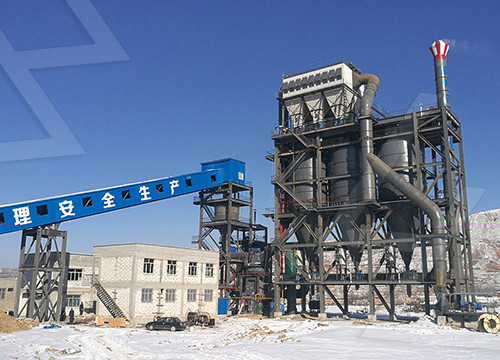
Advances in Mechanical Engineering 2021, Vol. 13(3) 1–9
20201022 A novelty heat transfer model was established from the point of energy view that can calculate the charge temperature of thermal conduction and heat
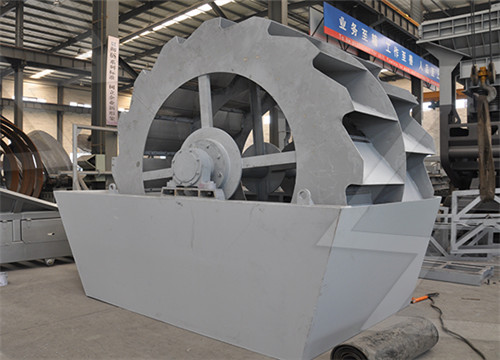
Ball milling synthesis and effects of infrared heat treating on
202311 Infrared (IR) heating is an exceptional and novel technique for heat treating various materials. It involves a much higher amount of surface heating and the diffusion
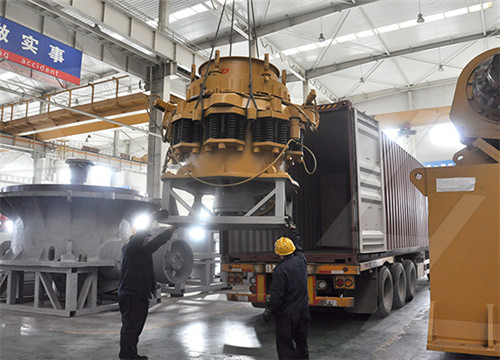
Ball milling synthesis and effects of infrared heat treating on
202311 It is mainly used for fusing coatings such as powder coating, paint drying, or printed layers [3]. It offers many benefits like energy efficiency, space saving, high
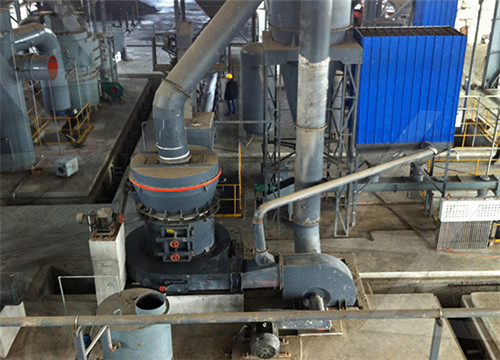
(PDF) Influence of Preliminary Heat Treatment and Ball
202111 This stone presents the results of a study of the effect of preliminary heat treatment and ball milling of aluminum powder on the cold spraying process and the
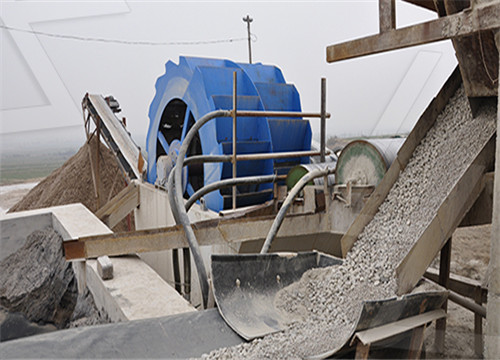
(PDF) Analysis on energy transfer during mechanical coating and ball
201361 PDF To investigate energy distribution and transfer during mechanical coating and ball milling, mechanical coating of Cu coatings on Al2O3 balls and a Find,
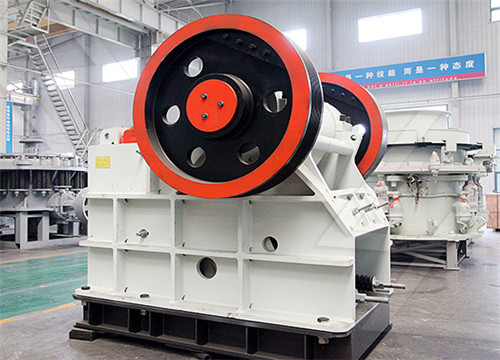
Effect of Different Milling Media for Surface Coating on
2020919 average velocity, force, and, kinetic energy of the milling media in a low and high energy ball mills. Keywords: dry surface coating; ball mill; copper; carbon
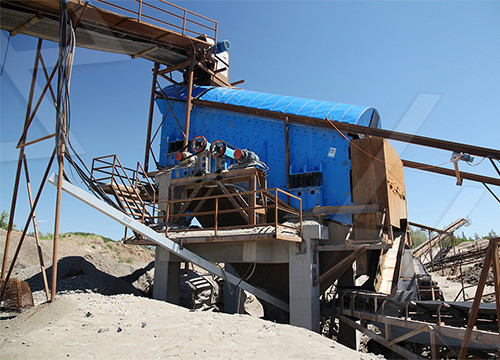
High-Energy Ball Milling an overview ScienceDirect Topics
High energy ball milling (HEBM) is an effective unconventional technique currently used in material synthesis and processing. From: Multifunctional and Nanoreinforced Polymers
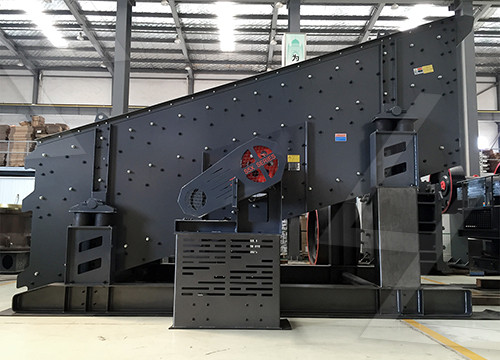
Materials Development Using High-Energy Ball
2022617 High-energy ball milling (HEBM) of powders is a complex process involving mixing, morphology changes, generation and evolution of defects of the crystalline lattice, and formation of new phases. This
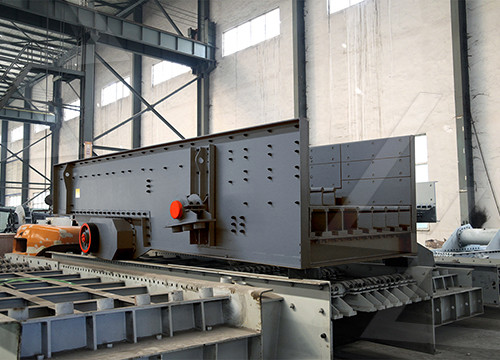
Ball End Mills: Which Coating is Right for You?
20231024 A Coating for Every Ball End Mill Purpose. Tool coatings are important for increasing the efficiency and longevity of ball end mills. It is important, however, to match the ideal coating with the intended application. In the proper application, the right coating will provide superior results, while also providing a greater ROI on the tool purchase.
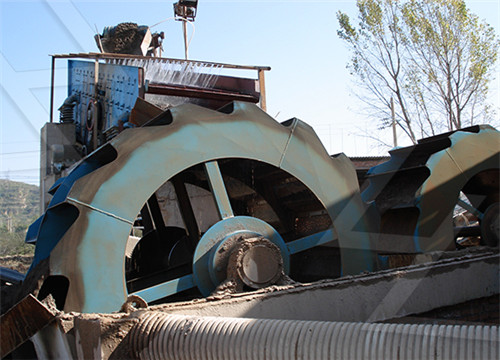
Ball Mill an overview ScienceDirect Topics
Quantum Nanostructures (QDs): An Overview. D. Sumanth Kumar, H.M. Mahesh, in Synthesis of Inorganic Nanomaterials, 2018 3.6.1.1 Ball Milling. A ball mill is a type of grinder used to grind and blend bulk material into QDs/nanosize using different sized balls. The working principle is simple; impact and attrition size reduction take place as the ball

Coatings Free Full-Text Effect of Different Milling Media
2020919 In recent years, nanocomposites have been fabricated by means of the mechanical alloying (MA) process that has been developed for obtaining metal matrix nanocomposites through the dry surface coating of metal powders [1,2,3].MA is very simple process and generic term for processing of metal powders in high energy ball mills and
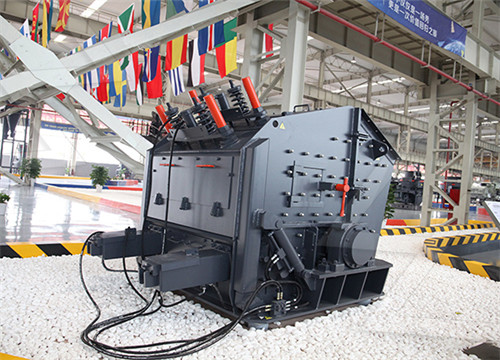
Hard Metal Machining RobbJack
Choosing the proper cutting tool is very important when machining hardened metal. There are three basic designs of cutters: ball end, corner radius (bullnose) or square end (Figure 1). The first choice in hard metal machining should be the ball end mill. The ball end mill should be used for roughing operations and most finishing operations.
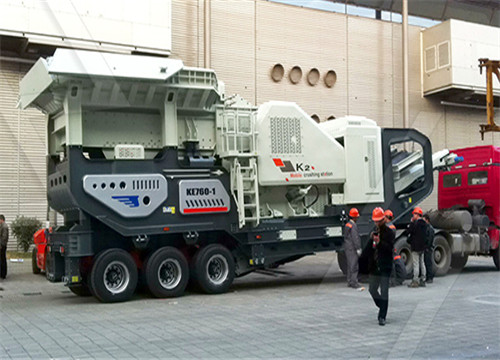
ATTRITOR GRINDING MILLS AND NEW DEVELOPMENTS
202122 1. The holding tank is jacketed for cooling or heating and acts as a heat sink. 2. The slurry passes through the grinding chamber very quickly (20-30 seconds per pass), therefore having less time to heat up. These advantages are very important when the grinding chamber is lined with plastic or rubber for metal-contamination-free processing.
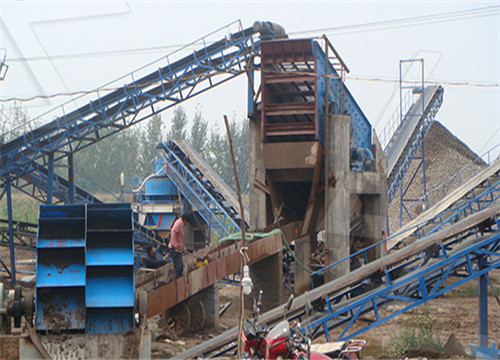
Review on vertical roller mill in cement industryits
202111 India is the world's second largest producer of cement and produces more than 8 per cent of global capacity. Due to the rapidly growing demand in various sectors such as defense, housing, commercial and industrial construction, government initiative such as smart citiesPMAY, cement production in India is expected to touch 550–600 million
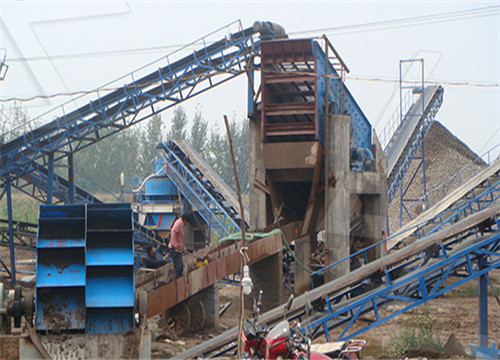
Ball Mill an overview ScienceDirect Topics
8.3.2.2 Ball mills. The ball mill is a tumbling mill that uses steel balls as the grinding media. The length of the cylindrical shell is usually 1–1.5 times the shell diameter (Figure 8.11 ). The feed can be dry, with less than 3% moisture to minimize ball coating, or slurry containing 20–40% water by weight.
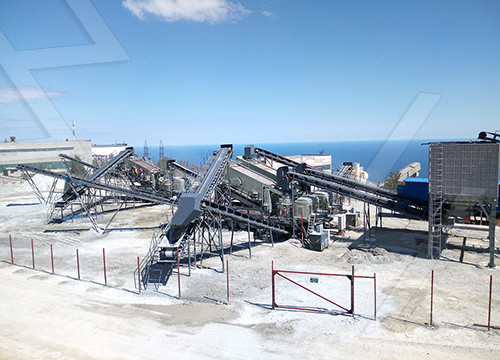
Coatings Free Full-Text Effect of Different Milling Media
2020919 This study investigated the effect of three different ball materials on the metal-based carbon nanotube (CNT) composites used as surface coatings on metal-powder to fabricate high-quality nanocomposites. The effect of ball material, different rotation speeds, and milling times on the coating characteristics of the metal-based

Temperature Reduction for Ball Mill Optimization Lechler US
Heat taken away by ventilation systems can accounts for roughly 20% of the total heat discharged by the ball mill. Improving that ventilation system brings more cool air into the inside of the ball bill, gradually reducing the internal temperature. However, the major benefit of using ball mills is the product fineness they can deliver.
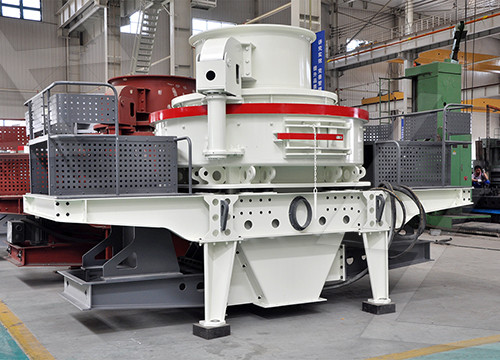
Common problems of ball mills and solutions to failures
20211129 When the ball mill rotates, the liner hits the grinding cylinder of the ball mill. Judge the position of the liner of the ball mill according to the sound, find out the loose bolts and tighten them separately. 2. The temperature of the bearings of the ball mill and the motor has risen, exceeding the requirements. Try to feel the bearing by hand.
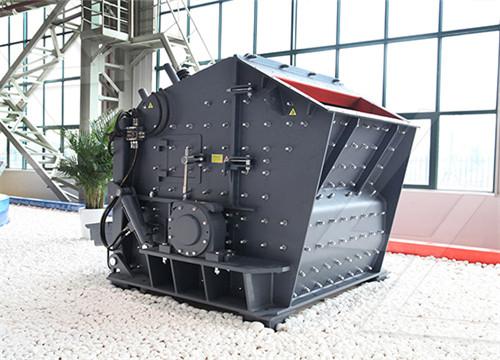
Ball Mill Dynamics PDF Mill (Grinding) Heat Treating
202234 3A: Ball Mill Fundamentals. 3A.1 Ball Mill Dynamics The basic objectives of ball milling is the size reduction of materials, called comminution. Size reduction in a ball mill is achieved primarily by the motion of the balls in the mill. By rotation, the mill elevates the ball charge and material and drops the load upon itself.. 3A.1.1 Comminution Mechanisms
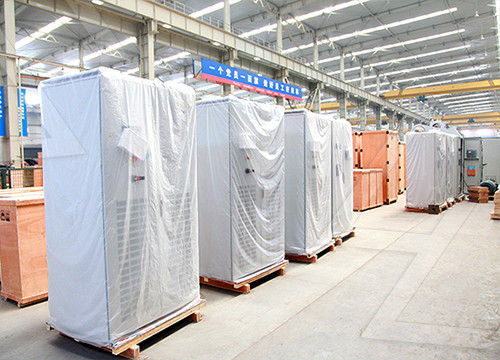
Ball milling: a green technology for the preparation and
The ball mill Ball milling is a mechanical technique widely used to grind powders into ne particles and blend materials.18 Being an environmentally-friendly, cost-effective technique, it has found wide application in industry all over the world. Since this mini-review mainly focuses on the conditions applied for the prep-
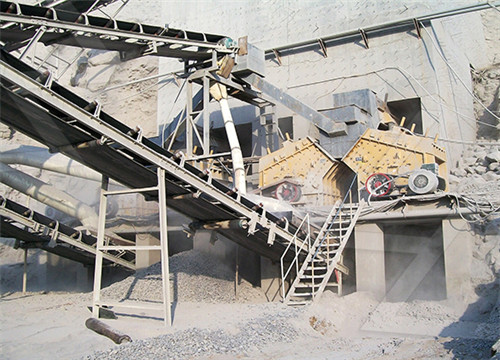
Top 5 product-specific milling technologies used in industrial
201777 Find the best size-reduction methods for achieving the product goal
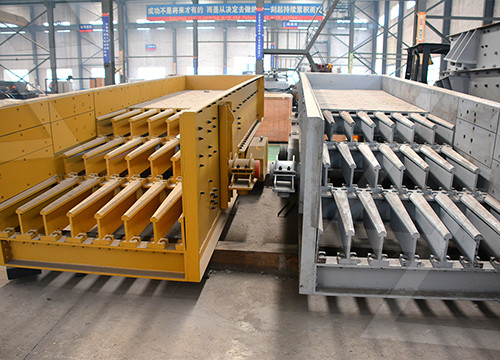
High-Energy Ball Milling an overview ScienceDirect Topics
5.3.2.4 High-Energy Ball Milling. High-energy ball milling is a ball milling process in which a powder mixture placed in a ball mill is subjected to high-energy collisions from the balls. High-energy ball milling, also called mechanical alloying, can successfully produce fine, uniform dispersions of oxide particles in nickel-base super alloys
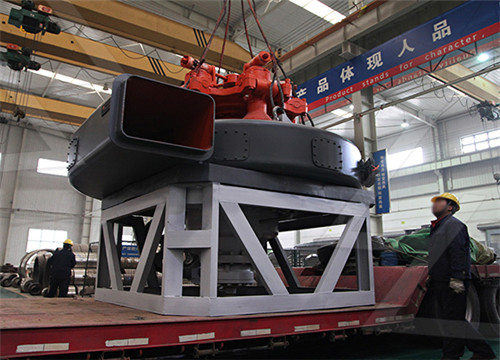
Ball Mill Balls Manufacturing Of High Quality Ball Mill Ball
Product Description. Ball mill balls are a type of ball used in ball mills, usually made of high-hardness materials such as steel, ceramics, hard alloys, etc. Ball mill steel balls is an important part of the ball mill, its main function is to carry out the grinding operation in the ball mill, and the material is crushed into the required size.
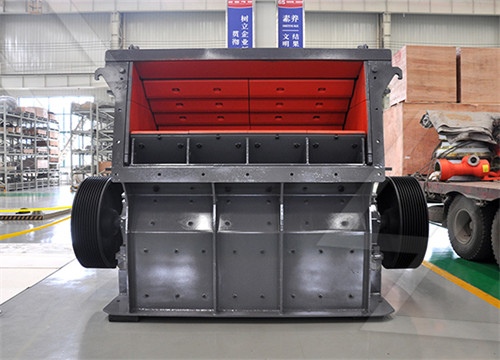
Coatings Free Full-Text Effect of Different Milling Media
In recent years, nanocomposites have been fabricated by means of the mechanical alloying (MA) process that has been developed for obtaining metal matrix nanocomposites through the dry surface coating of metal powders [1,2,3].MA is very simple process and generic term for processing of metal powders in high energy ball mills and economically viable
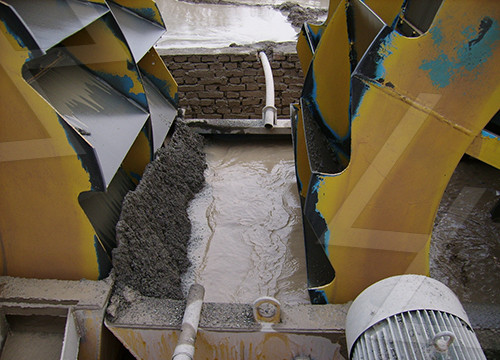
Influence of preliminary heat treatment and ball milling of
202011 This stone presents the results of a study of the influence of preliminary heat treatment (pressure 10 −3 MPa, temperature 390 K for 12 h) and ball milling (milling time 90 s, ball to powder ratio 160:30) of copper powder on the deposition process and coating properties (porosity and microhardness). It was shown that coatings sprayed
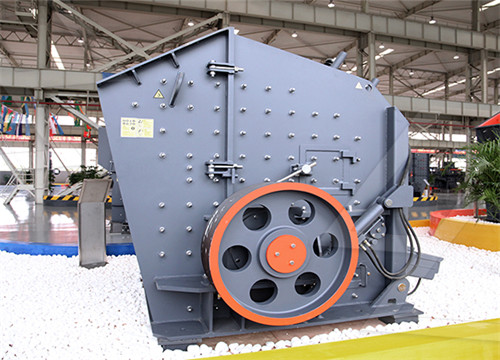
Ball milling synthesis and effects of infrared heat treating on
202311 The milling process was carried out using a high-energy planetary ball mill with a container and balls of hardened steel. The vials were designed to keep argon gas pressure at 100 mbar (partial pressure to maintain the vials sealed). The milling speed and the ball to powder weight ratio (BPR) were adjusted to 250 rpm and 10:1, respectively.
كسارة الفك المحمولة حفرة مفتوحة
الباريت مصنع التركيز
كسارة الحجر pabrik di odisha
بيع كسارات تعدين الذهب
فرن عمودي بيليه الحديد
الصورة دلو طاحونة كسارة
آلة تكسير الجرافيت
letz buhr مطحنة موديل 50 نوع أ
مطاحن الكرة لطحن بيتكوك
استخدام الهندسة الميكانيكية في البناء المدني
الأسمنت سهم السعر اليوم
أفضل الكسارات الصخرية
طاحون الشرالحلقت
شراء كسارات الحجر آلات 02
كسارة مخروط tmobile لمصنع الذهب
spesifikasi تهتز شاشة cpo
الحجر كسارات مزادات
قمة الحفر آلة طحن
تستخدم اللحوم المطاحن
D و M التعدين لوازم بريتوريا غوتنغ
كسارة متنقلة Bolivia للبيع البرازيل
الصابورة فرز النباتات أيون specifi
لوحة كسارة الفك المتنقلة المتنقلة في كسر الكوع
الألغام dhariyawad الحجر الجيري
طحن دان الفرز ndustri
تجهيز الحجر الجيري الرسم البياني مصنع
حول لدينا
تأسست شركة Henan Lrate للعلوم والتكنولوجيا المحدودة التي تصنع معدات التكسير والطحن الكبيرة والمتوسطة الحجم في عام 1987. وهي شركة مساهمة حديثة مع البحث والتصنيع والمبيعات معًا.
على مدار أكثر من 30 عامًا ، تلتزم شركتنا بنظام الإدارة العلمية الحديث والتصنيع الدقيق والريادة والابتكار. الآن أصبحت LIMING رائدة في صناعة تصنيع الآلات المحلية والخارجية.