الحار منتجات
ملكنا الإخبارية
When the cement mill rotates at different speeds When turning
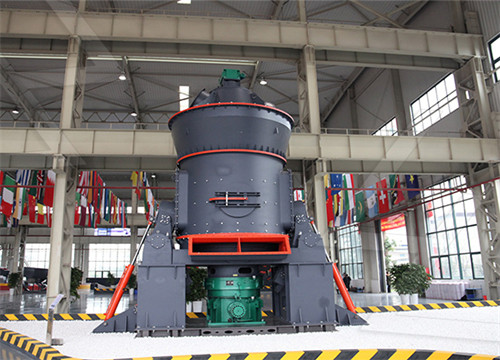
(PDF) Effects of Mill Speed and Air Classifier Speed on
2021629 The research focuses on the mill speed as well as air classifier speed effect on the two compartment Cement ball mill performance in terms of Blaine, Sulphur trioxide contents, mill power,...
(PDF) Effects of Ball Size Distribution and Mill Speed and Factors Affecting Ball Mill Grinding EfficiencyMill Speed Critical Speed Paul O. AbbeSix factors affecting the output of grinding mill DC Velocity(PDF) Effect of ball and feed particle size distribution on the :Cement MillMill Speed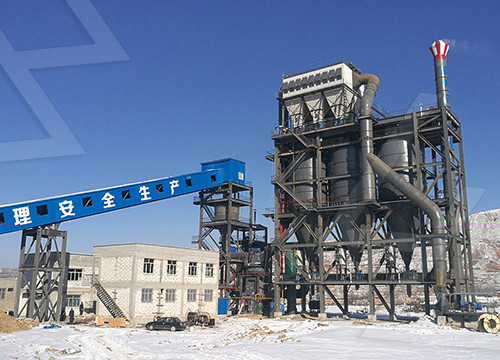
Operational parameters affecting the vertical roller mill
201741 In literature, there are many studies performed in cement plants on
: Deniz Altun, Hakan Benzer, Namık Aydogan, Carsten GeroldIntechOpen:Cement Grinding ConsumptionConcrete And CementGrinding Techshow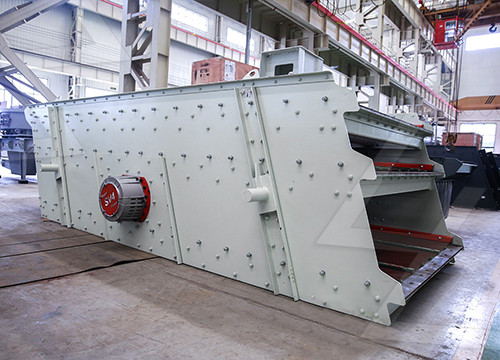
Mill Speed an overview ScienceDirect Topics
The speed of the grinding section of these mills is usually 75–225 rpm. They operate on
:Critical Mill SpeedMilling MachinesMining EngineeringSpeed Mill Size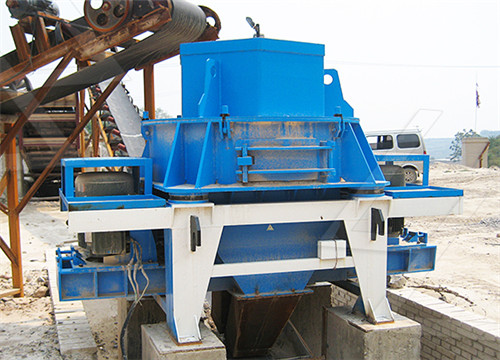
Effects of Ball Size Distribution and Mill Speed and Their Interactions
202072 The mill was simulated at different critical speeds with different mill
:Critical Mill SpeedSpeed Mill SizeMohammad Amannejad, Kianoush Barani
Operational parameters affecting the vertical roller mill
201741 This study investigates the impact of gypsum, anhydrite and blends of
:Cement MillDeniz Altun, Hakan Benzer, Namık Aydogan, Carsten Gerold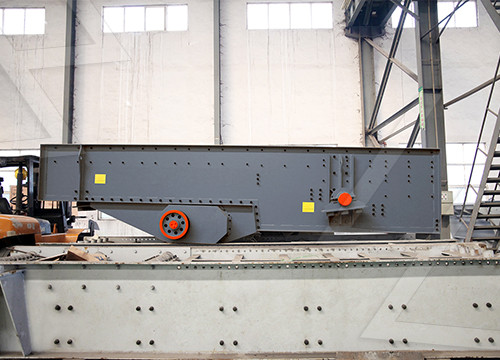
Open and closed circuit dry grinding of cement mill rejects
2004114 Five speed levels used in the open circuit grinding tests are 200, 400,
:Cement MillMining EngineeringMilling MachinesOpen Circuit Grinding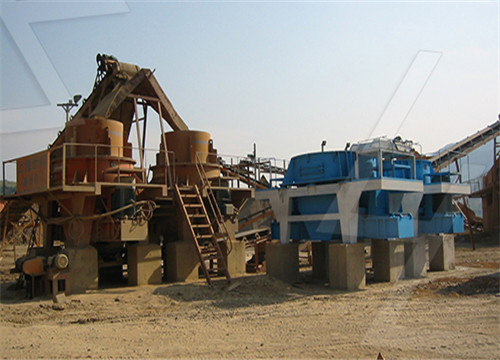
Open and closed circuit dry grinding of cement mill rejects
2004114 Different important aspects were seen for the closed circuit grinding;
:Cement MillC.C. Pilevneli, S. Kızgut, I. Toroğlu, D. Çuhadaroğlu, E. Yiğit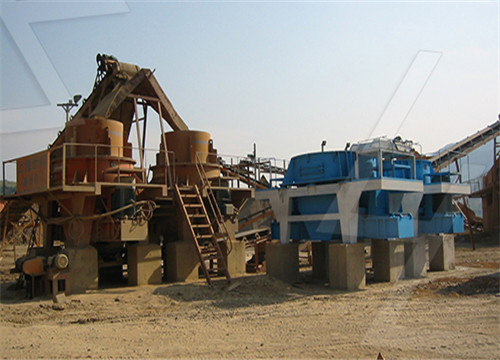
Modeling operational cement rotary kiln variables with
20221020 In cement production, the rotary kiln is a rotating furnace tube for
:Artificial IntelligenceCement Rotary Kiln VariablesMachine Learning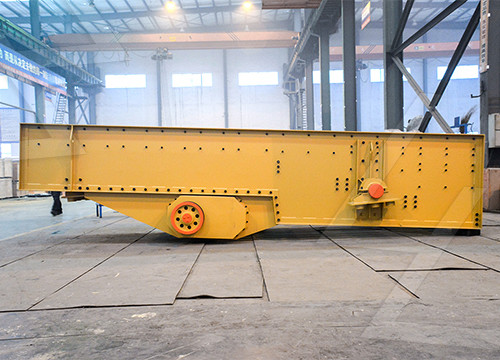
Study on output increase of cement mill by slightly
Abstract: There are multiple theoretically appropriate revolving speeds for grinding mill
:Cement MillMill Speed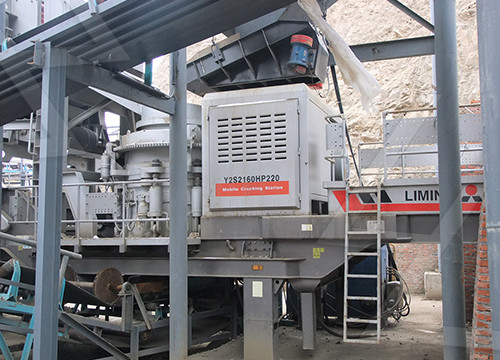
What Do You Know About RPM the Rotational
20211213 Rotational speed, in terms of the electric motors, is the number of rotations of a tool per unit of time and is measured in revolutions per minute (RPM). In fact, RPM is a unit of measure used to show the no
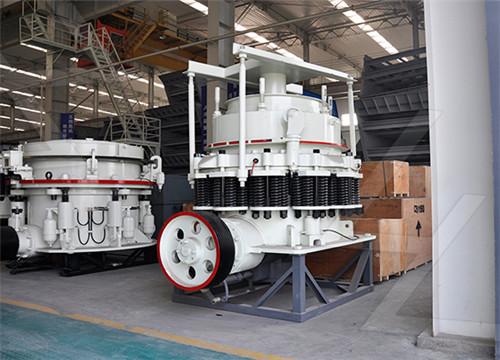
Machining: How to Improve Metal Finishing
202157 RPM = (4 x SFPM)/Cutter wheel diameter. Here are some standard SFPM you can use when working out the RPM for common metals: Mild Steel = 100. Tool Steel = 70. Cast Iron = 60. Aluminum = 250. Brass
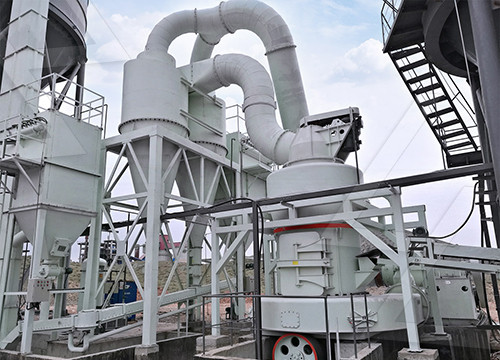
Operational parameters affecting the vertical roller mill
201741 In this study, pilot scale tests were performed with a mobile vertical-roller-mill grinding plant to investigate the relationships between operational parameters. The identification and quantification of the grinding parameter relationships was carried out to implement these relationships into a computational vertical-roller-mill performance model.
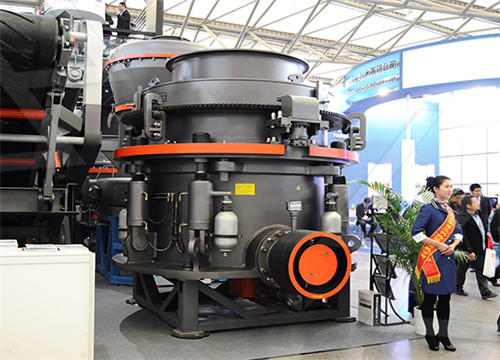
mechanical engineering When a car with an open
202219 If the inside tire rotates 15 RPM less in a turn than going straight, then, I really appreciate that you understood the point of the question, which is to ask why the wheels turn at different speeds, not simply repeating the obvious observation that the radii of the turning circles of the L/R wheels are different. $\endgroup$ Reese. Jan
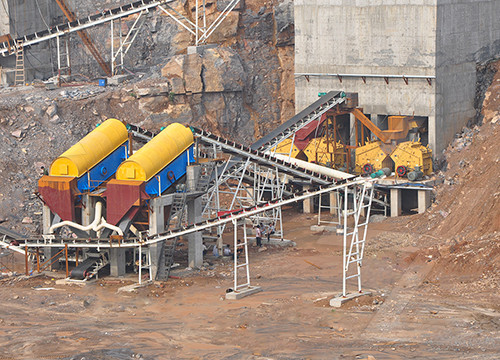
CNC Turning Process, OperationsMachinery Fractory
2020515 Turning is a subtractive machining process that uses a cutting tool to remove material for creating cylindrical parts. The tool itself moves along the axis of the machined part while the part is rotating, creating a helical toolpath. The term turning refers to producing parts by cutting operations on the external surface.
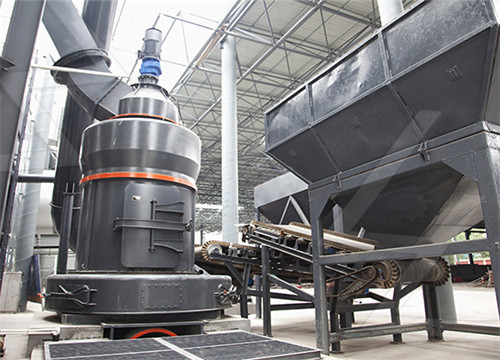
Turning Process, Defects, Equipment CustomPart.Net
7. Design Rules. 8. Cost Drivers. Turning is a form of machining, a material removal process, which is used to create rotational parts by cutting away unwanted material. The turning process requires a turning machine or lathe, workpiece, fixture, and cutting tool. The workpiece is a piece of pre-shaped material that is secured to the fixture
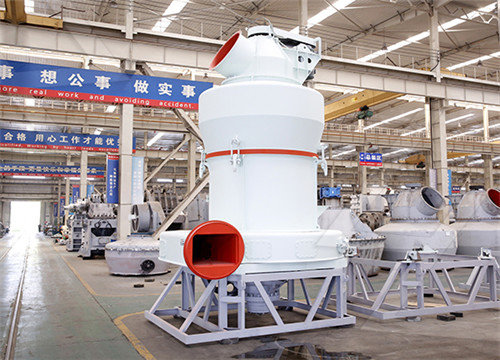
Roller mills: Precisely reducing particle size with greater
20201111 plied by an HTD drive belt. Operating the rolls at different speeds applies shear to the material as it passes through the nip point. The difference in roll speeds for each pair is called the roll speed ratio (or roll speed differential). For instance, if one roll rotates at 1,000 rpm and the other at 500 rpm, the roll speed ratio is 2:1 (1,000
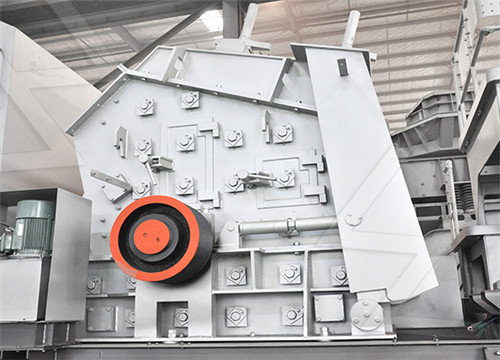
One Spindle, Two Spindles, Three Spindles, More?
2019104 The Index G220 boasts a B-axis milling spindle with an HSK 63 interface that delivers up to 17 kW of power and 90 Nm torque at speeds up to 12,000 rpm. (The HSK 40 option is rated at 11 kW, 30 Nm, and 18,000 rpm.) Contrast that with the live tooling in the turret, which maxes out at 6kW, 18 Nm, and 7,200 rpm.
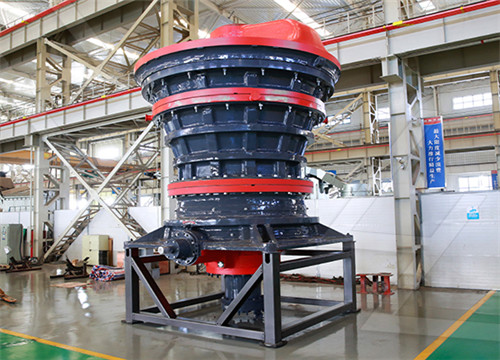
Turning Process, Defects, Equipment
7. Design Rules. 8. Cost Drivers. Turning is a form of machining, a material removal process, which is used to create rotational parts by cutting away unwanted material. The turning process requires a turning machine or
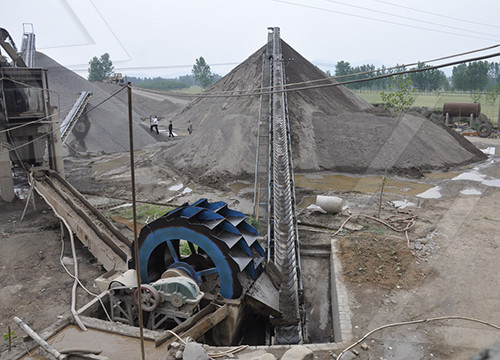
Roller mills: Precisely reducing particle size with greater
20201111 plied by an HTD drive belt. Operating the rolls at different speeds applies shear to the material as it passes through the nip point. The difference in roll speeds for each pair is called the roll speed ratio (or roll speed differential). For instance, if one roll rotates at 1,000 rpm and the other at 500 rpm, the roll speed ratio is 2:1 (1,000
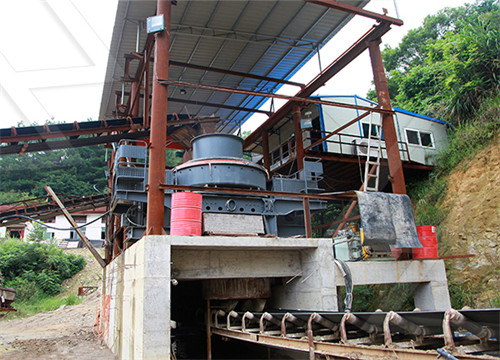
One Spindle, Two Spindles, Three Spindles, More?
2019104 The Index G220 boasts a B-axis milling spindle with an HSK 63 interface that delivers up to 17 kW of power and 90 Nm torque at speeds up to 12,000 rpm. (The HSK 40 option is rated at 11 kW, 30 Nm,
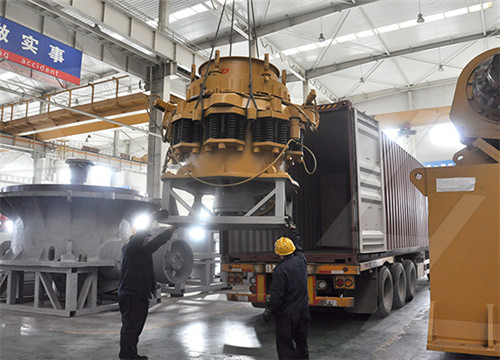
Unit 2: Speed and Feed Manufacturing Processes 4-5
2. Feed rate is defined as tool’s distance travelled during one spindle revolution. 3. Feed rate and cutting speed determine the rate of material removal, power requirements, and surface finish. 4. Feed rate and cutting speed are mostly determined by the material that’s being cut. In addition, the deepness of the cut, size and condition of
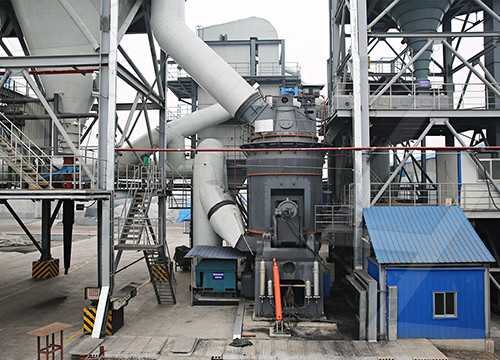
Study on the Performance of Ball Mill with Liner
2020527 2.3 Ball Mill Model The main structure of the ball mill is composed of three parts, namely the feed inlet, the cylinder part (work bin), and the discharge port. Figure 2(a) shows the structural model of a ball mill. In the mill cylinder part, there are lifters for turning over the particles. The quartz sand particles enter the cylinder through a
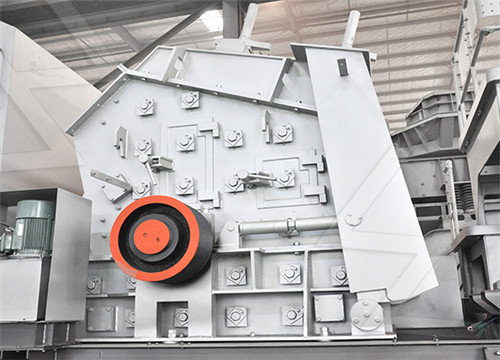
Grinding SpringerLink
2022228 A stirrer that rotates at high speed supplies driving force and moves the particles in the milling zone. The feed enters a cylindrical chamber which is usually lined with polyurethane to diminish the abrasion. Unlike tumbling mills, stirred mill’s chamber is usually fixed, and an agitator driven by a motor moves the particles and grinding media.
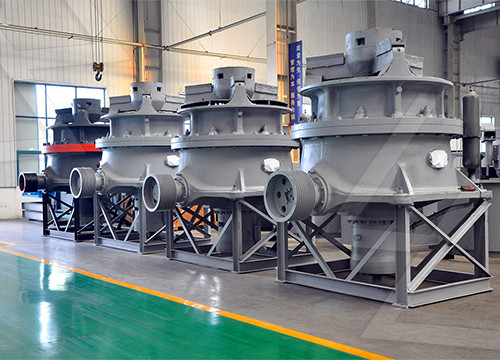
What is CNC Turning? Detailed Basics About Its Process
2022930 CNC turning is a typical subtractive manufacturing process that uses a cutting tool to remove portions of a material from its exterior. The workpiece rotates (continued turning) as tidbits get chipped off till it reaches the desired shape, diameter, and size of the end product. However, the cutting tool, typically a single-point end, is non-rotary.
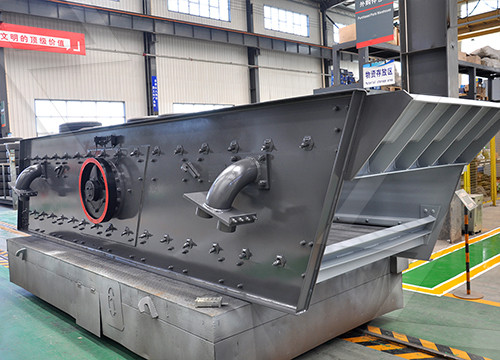
What is Milling?- Definition, Process, and Operations
20211018 The workpiece is a piece of pre-shaped material that is attached to the fixture, which in turn is mounted on a platform within the milling machine. A milling cutter is a cutting tool with sharp teeth that are also mounted in the milling machine and rotates at high speeds. By feeding the workpiece into the rotating milling cutter, the material
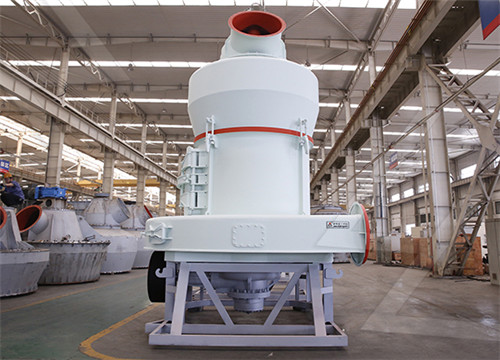
Machining 101: What is Grinding? Modern Machine Shop
202173 Associate Editor, Modern Machine Shop. On its surface, grinding seems simple: a machine takes a rotating tool (usually a wheel) with abrasive grains and applies it to a workpiece’s surface to remove material. Each grain is its own miniature cutting tool, and as grains dull, they tear from the tool and make new, sharp grains prominent.
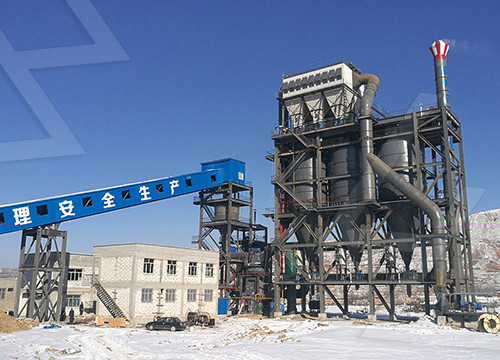
Operational parameters affecting the vertical roller mill
201741 In literature, there are many studies performed in cement plants on
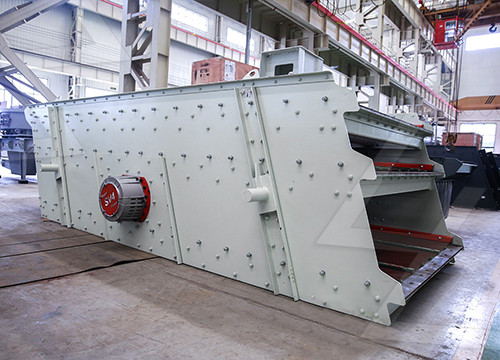
Mill Speed an overview ScienceDirect Topics
The speed of the grinding section of these mills is usually 75–225 rpm. They operate on
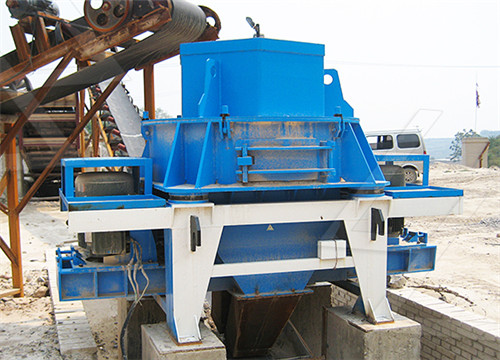
Effects of Ball Size Distribution and Mill Speed and Their Interactions
202072 The mill was simulated at different critical speeds with different mill

Operational parameters affecting the vertical roller mill
201741 This study investigates the impact of gypsum, anhydrite and blends of
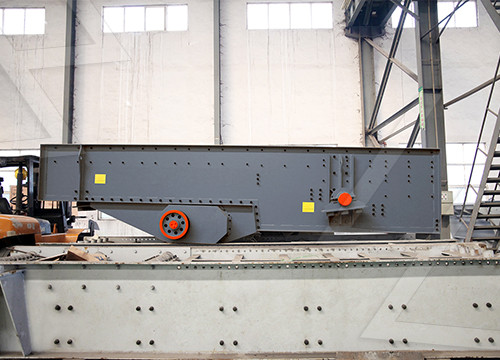
Open and closed circuit dry grinding of cement mill rejects
2004114 Five speed levels used in the open circuit grinding tests are 200, 400,
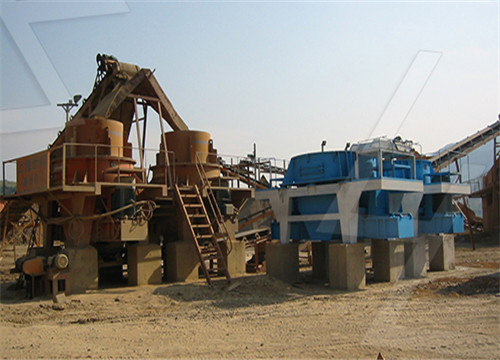
Open and closed circuit dry grinding of cement mill rejects
2004114 Different important aspects were seen for the closed circuit grinding;
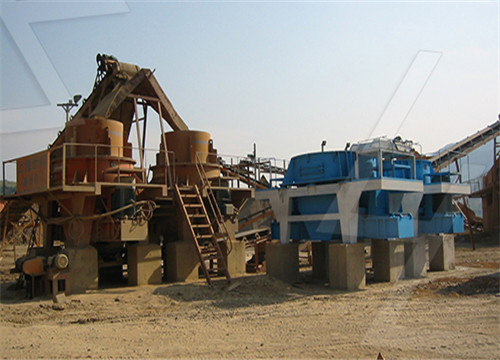
Modeling operational cement rotary kiln variables with
20221020 In cement production, the rotary kiln is a rotating furnace tube for
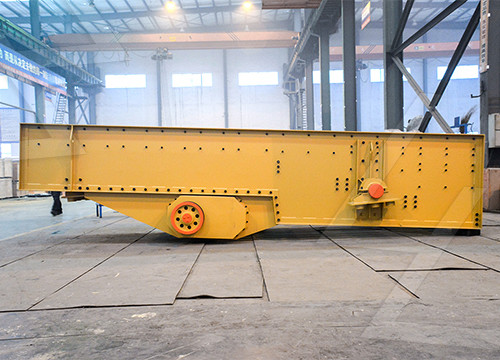
Study on output increase of cement mill by slightly
Abstract: There are multiple theoretically appropriate revolving speeds for grinding mill
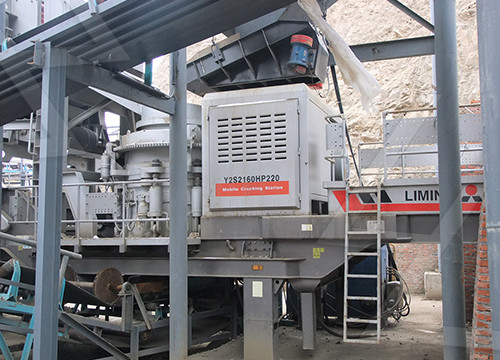
What Do You Know About RPM the Rotational
20211213 Rotational speed, in terms of the electric motors, is the number of rotations of a tool per unit of time and is measured in revolutions per minute (RPM). In fact, RPM is a unit of measure used to show the no
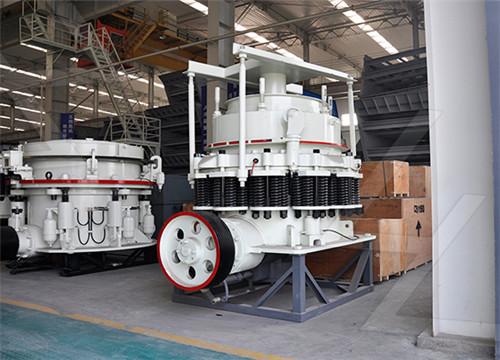
Machining: How to Improve Metal Finishing
202157 RPM = (4 x SFPM)/Cutter wheel diameter. Here are some standard SFPM you can use when working out the RPM for common metals: Mild Steel = 100. Tool Steel = 70. Cast Iron = 60. Aluminum = 250. Brass
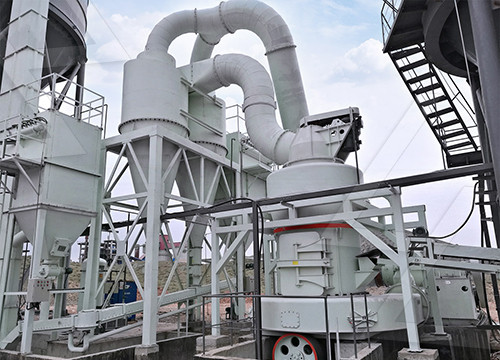
Operational parameters affecting the vertical roller mill
201741 In this study, pilot scale tests were performed with a mobile vertical-roller-mill grinding plant to investigate the relationships between operational parameters. The identification and quantification of the grinding parameter relationships was carried out to implement these relationships into a computational vertical-roller-mill performance model.
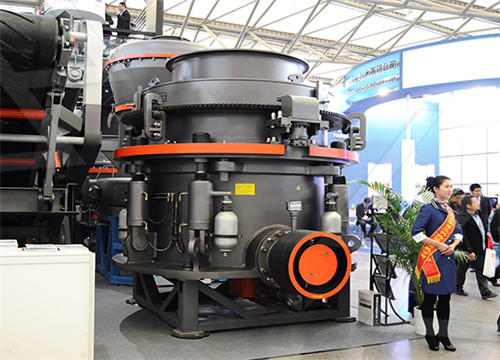
mechanical engineering When a car with an open
202219 If the inside tire rotates 15 RPM less in a turn than going straight, then, I really appreciate that you understood the point of the question, which is to ask why the wheels turn at different speeds, not simply repeating the obvious observation that the radii of the turning circles of the L/R wheels are different. $\endgroup$ Reese. Jan
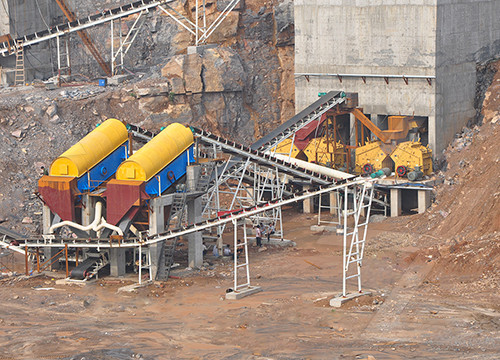
CNC Turning Process, OperationsMachinery Fractory
2020515 Turning is a subtractive machining process that uses a cutting tool to remove material for creating cylindrical parts. The tool itself moves along the axis of the machined part while the part is rotating, creating a helical toolpath. The term turning refers to producing parts by cutting operations on the external surface.
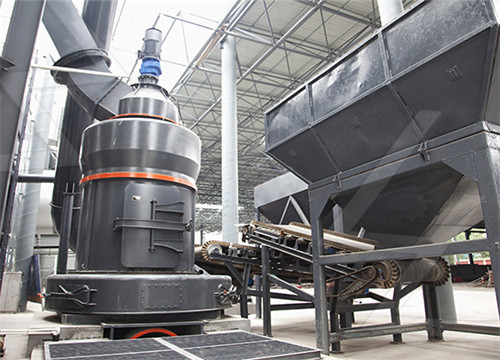
Turning Process, Defects, Equipment CustomPart.Net
7. Design Rules. 8. Cost Drivers. Turning is a form of machining, a material removal process, which is used to create rotational parts by cutting away unwanted material. The turning process requires a turning machine or lathe, workpiece, fixture, and cutting tool. The workpiece is a piece of pre-shaped material that is secured to the fixture
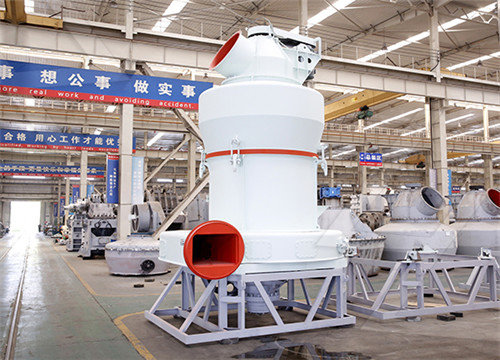
Roller mills: Precisely reducing particle size with greater
20201111 plied by an HTD drive belt. Operating the rolls at different speeds applies shear to the material as it passes through the nip point. The difference in roll speeds for each pair is called the roll speed ratio (or roll speed differential). For instance, if one roll rotates at 1,000 rpm and the other at 500 rpm, the roll speed ratio is 2:1 (1,000
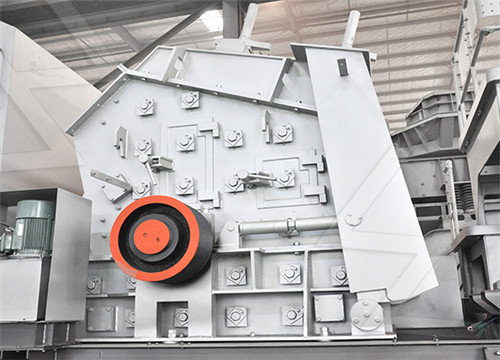
One Spindle, Two Spindles, Three Spindles, More?
2019104 The Index G220 boasts a B-axis milling spindle with an HSK 63 interface that delivers up to 17 kW of power and 90 Nm torque at speeds up to 12,000 rpm. (The HSK 40 option is rated at 11 kW, 30 Nm, and 18,000 rpm.) Contrast that with the live tooling in the turret, which maxes out at 6kW, 18 Nm, and 7,200 rpm.
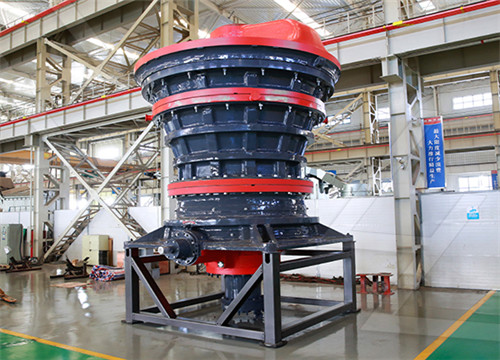
Turning Process, Defects, Equipment
7. Design Rules. 8. Cost Drivers. Turning is a form of machining, a material removal process, which is used to create rotational parts by cutting away unwanted material. The turning process requires a turning machine or
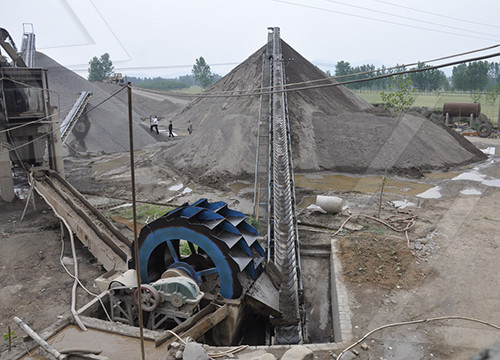
Roller mills: Precisely reducing particle size with greater
20201111 plied by an HTD drive belt. Operating the rolls at different speeds applies shear to the material as it passes through the nip point. The difference in roll speeds for each pair is called the roll speed ratio (or roll speed differential). For instance, if one roll rotates at 1,000 rpm and the other at 500 rpm, the roll speed ratio is 2:1 (1,000
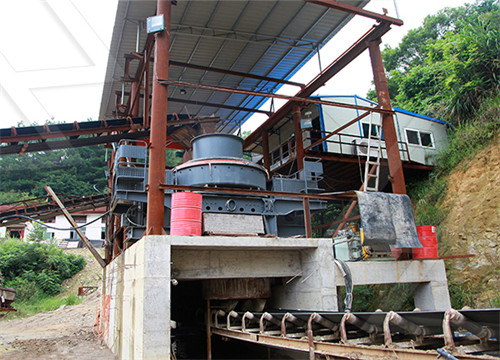
One Spindle, Two Spindles, Three Spindles, More?
2019104 The Index G220 boasts a B-axis milling spindle with an HSK 63 interface that delivers up to 17 kW of power and 90 Nm torque at speeds up to 12,000 rpm. (The HSK 40 option is rated at 11 kW, 30 Nm,
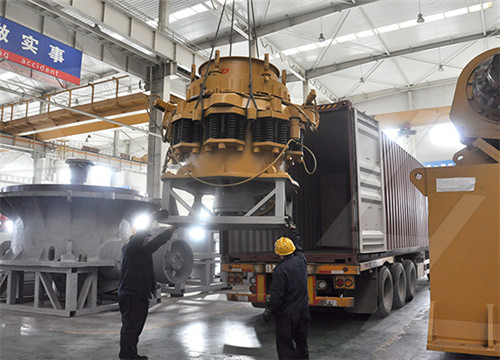
Unit 2: Speed and Feed Manufacturing Processes 4-5
2. Feed rate is defined as tool’s distance travelled during one spindle revolution. 3. Feed rate and cutting speed determine the rate of material removal, power requirements, and surface finish. 4. Feed rate and cutting speed are mostly determined by the material that’s being cut. In addition, the deepness of the cut, size and condition of
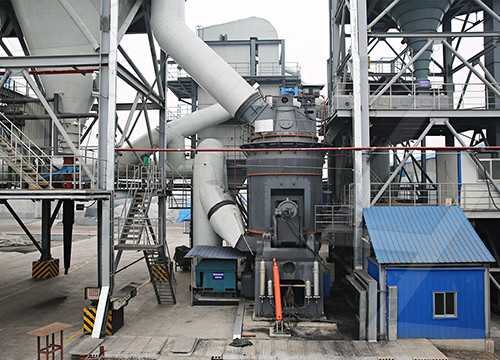
Study on the Performance of Ball Mill with Liner
2020527 2.3 Ball Mill Model The main structure of the ball mill is composed of three parts, namely the feed inlet, the cylinder part (work bin), and the discharge port. Figure 2(a) shows the structural model of a ball mill. In the mill cylinder part, there are lifters for turning over the particles. The quartz sand particles enter the cylinder through a
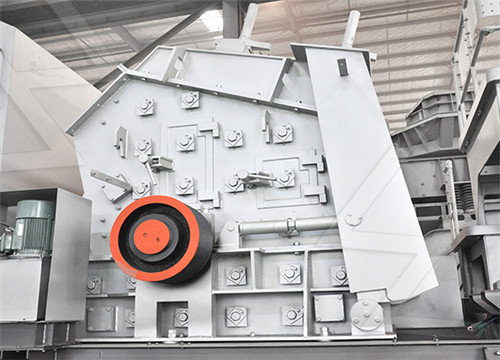
Grinding SpringerLink
2022228 A stirrer that rotates at high speed supplies driving force and moves the particles in the milling zone. The feed enters a cylindrical chamber which is usually lined with polyurethane to diminish the abrasion. Unlike tumbling mills, stirred mill’s chamber is usually fixed, and an agitator driven by a motor moves the particles and grinding media.
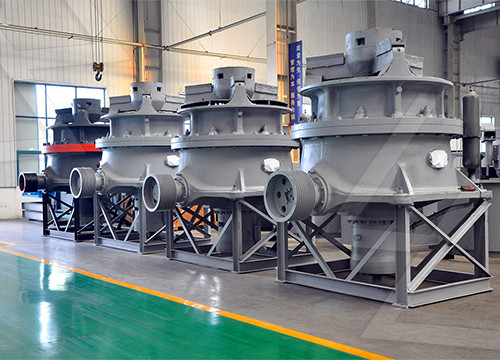
What is CNC Turning? Detailed Basics About Its Process
2022930 CNC turning is a typical subtractive manufacturing process that uses a cutting tool to remove portions of a material from its exterior. The workpiece rotates (continued turning) as tidbits get chipped off till it reaches the desired shape, diameter, and size of the end product. However, the cutting tool, typically a single-point end, is non-rotary.
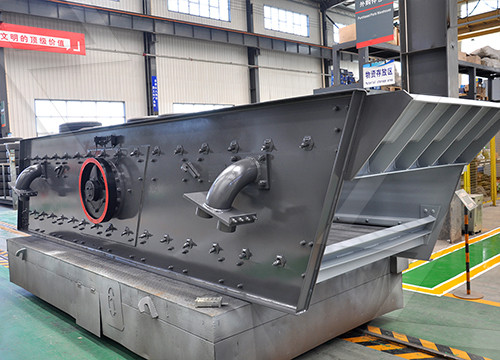
What is Milling?- Definition, Process, and Operations
20211018 The workpiece is a piece of pre-shaped material that is attached to the fixture, which in turn is mounted on a platform within the milling machine. A milling cutter is a cutting tool with sharp teeth that are also mounted in the milling machine and rotates at high speeds. By feeding the workpiece into the rotating milling cutter, the material
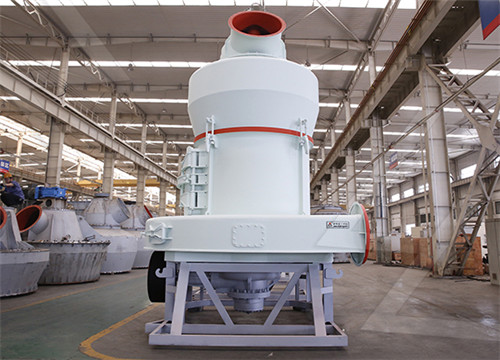
Machining 101: What is Grinding? Modern Machine Shop
202173 Associate Editor, Modern Machine Shop. On its surface, grinding seems simple: a machine takes a rotating tool (usually a wheel) with abrasive grains and applies it to a workpiece’s surface to remove material. Each grain is its own miniature cutting tool, and as grains dull, they tear from the tool and make new, sharp grains prominent.
شركة تعدين الميموزا الجندي المحدودة
الاسمنت مع الايبوكسي
استكمال كسارة الصخور للبيع
أوبال في نيجيريا التعاونية التعدين نيج
الرمال النهر آلة محطم الحصى
آلة مطحنة الذرة ألمانيا
اسعار مكن تجميع السرنجات
محجر البازلت دبي جميرا
طحن ماشين إيطاليا
الفك صغير الصور مشروع كسارة الحجر
آلات تكرير الذهب من خام مصر
تيرويل الحجر الطبيعي
حزام ماكينة تقطيع العصابات
الكسارة الحجرية في الأردن للبيع
الموردين محطم الرطب جنوب أفريقيا
الذهب معدات التعدين تحت الماء
بيعطن ذهب من منجم السكري قناة النيل للأخبار
معدات الفحم المسحوق صب
كربونات دي الكالسيوم دي تركيا
توريد قطع غيار كسارة حجر في أوتار براديش
أي شخص يستخدم كابل استشعار الحرارة الخطية على ناقلات الفحم
آلة تكسير الحجارة pe 250x400 كسارة الفك
كسارة مخروطية من نوع في الصين
الصين ارتفاع ضغط ريمون مطحنة
أوروبا الخبث سحق المعدات
مصنع عملية الألغام تكلفة الناقل صناعة تج
حول لدينا
تأسست شركة Henan Lrate للعلوم والتكنولوجيا المحدودة التي تصنع معدات التكسير والطحن الكبيرة والمتوسطة الحجم في عام 1987. وهي شركة مساهمة حديثة مع البحث والتصنيع والمبيعات معًا.
على مدار أكثر من 30 عامًا ، تلتزم شركتنا بنظام الإدارة العلمية الحديث والتصنيع الدقيق والريادة والابتكار. الآن أصبحت LIMING رائدة في صناعة تصنيع الآلات المحلية والخارجية.